Table of contents
Four point contact bearings
- Bearing design
- Load carrying capacity
- Compensation of angular misalignments
- Lubrication
- Sealing
- Speeds
- Noise
- Temperature range
- Cages
- Internal clearance
- Dimensions, tolerances
- Suffixes
- Structure of bearing designation
- Dimensioning
- Minimum load
- Design of bearing arrangements
- Mounting and dismounting
- Legal notice regarding data freshness
- Further information
Four point contact bearings
Four point contact bearings are particularly suitable where:
- Predominantly axial loads must be supported ➤ section
- The axial design envelope is not sufficient for double row radial angular contact ball bearings
- Radial forces must be supported by a separate radial bearing ➤ Figure
- Axial forces occur in both directions and a close axial clearance is required in conjunction with a small bearing width, e. g. in gearbox engineering.
Four point contact bearing and double row angular contact ball bearing – comparison of design envelope B = bearing width |
![]() |
Bearing design
Design variants
Four point contact bearings are available as:
Bearings of basic design
Comparable, in terms of product design, with single row radial angular contact ball bearings
Four point contact bearings are single row, non self-retaining radial ball bearings. They are similar in their structure to single row radial angular contact ball bearings; the raceways on the inner rings are, however, designed such that they can support axial loads in both directions ➤ Figure and ➤ section. The centre points of curvature of the arc-shaped raceways on the inner and outer ring are offset relative to each other in such a way that the balls are in contact with the bearings at four points under radial load ➤ Figure and ➤ section.
Smaller axial section height than double row angular contact ball bearings
These bearings have solid outer rings, split inner rings and ball and cage assemblies with brass or polyamide cages ➤ section. The two-piece inner ring allows a large complement of balls to be accommodated in the bearing. The inner ring halves are matched to the particular bearing and must not be interchanged with those of other bearings of the same size. In an axial direction, four point contact bearings are considerably narrower than, for example, double row angular contact ball bearings.
Four point contact bearing of basic design α = nominal contact angle M1, M2 = centres of curvature of outer ring raceway Fr = radial load Fa = axial load
|
![]() |
Bearings with retaining slots in the outer ring
The retaining slots allow simple location of the bearing in the housing
Four point contact bearings are often combined with a radial bearing and used as an axial bearing with radial clearance in a housing ➤ Figure, ➤ section. For quick and secure location of the bearings in the housing, larger bearings therefore have two retaining slots in one end face of the outer ring offset by 180° ➤ Figure. Locking pins engage in these retaining slots and locate the outer ring in the housing.
Four point contact bearing used as an axial bearing, radial clearance on outer ring, axial force flow
|
![]() |
X-life premium quality
Four point contact bearings are available in certain sizes as X-life bearings. These bearings exhibit considerably higher performance than standard four point contact bearings ➤ Figure. This is achieved, for example, through the modified internal construction, higher surface quality of the contact surfaces and optimised cage design, as well as through the improved quality of the steel and rolling elements.
Advantages
Increased customer benefits due to X-life
The technical enhancements offer a range of advantages, such as:
- a more favourable load distribution in the bearing and thus a higher dynamic load carrying capacity of the bearings ➤ Figure
- quieter running
- running with reduced friction and greater energy efficiency
- lower heat generation in the bearing
- higher possible speeds
- lower lubricant consumption and, consequently, longer maintenance intervals
- a measurably longer operating life
- high operational security
- compact, environmentally-friendly bearing arrangements.
Lower operating costs, higher machine availability
In conclusion, these advantages improve the overall cost-efficiency of the bearing position significantly and thus bring about a sustainable increase in the efficiency of the machine and equipment.
Suffix XL
X-life four point contact bearings include the suffix XL in the designation ➤ Table, ➤ Figure and ➤ dimension table.
Comparison of basic dynamic load rating Cr – bearing series QJ3..-XL, bore code 5 to 14, with a bearing which is not of X-life quality Cr = basic dynamic load rating
|
![]() |
Areas of application
Wide application range
Due to their special technical features, X-life four point contact bearings are highly suitable for bearing arrangements in:
- compressors
- fluid and hydraulic pumps
- automotive chassis and gearboxes
- gearboxes for industrial, rail and wind turbine applications
- agricultural vehicles and equipment.
X-life indicates a high product performance density and thus a particularly significant benefit to the customer. Further information on X-life ➤ link.
Load carrying capacity
Capable of supporting high axial loads in both directions
Due to the design of the raceways with their high shoulders, the large nominal contact angle of α0 = 35° and the large number of rolling elements, four point contact bearings have a very high axial load carrying capacity. They are suitable for alternating, purely axial loads or predominantly axial load. The balls are in contact with the inner ring and outer ring each at one point only, as is the case with a single row angular contact ball bearing under axial load➤ Figure.
The radial load carrying capacity of the bearings is low. If predominantly radial load is present, four point contact bearings should not be used due to the higher friction in the four point contact.
Compensation of angular misalignments
Four point contact bearings cannot compensate misalignments
Four point contact bearings are not suitable for the compensation of angular misalignments due to housing deformations or shaft deflections. The possible skewing of the inner ring in relation to the outer ring depends, for example, on the bearing load, the operating clearance and the bearing size, and is very small.
Skewing of the bearing rings increases the running noise, places increased strain on the cages and has a harmful influence on the operating life of the bearings.
Lubrication
Oil or grease lubrication
The bearings are not greased. They must be lubricated with oil or grease.
Compatibility with plastic cages
When using bearings with plastic cages, compatibility between the lubricant and the cage material must be ensured if synthetic oils, lubricating greases with a synthetic oil base or lubricants containing a high proportion of EP additives are used.
Observe oil change intervals
Aged oil and additives in the oil can impair the operating life of plastics at high temperatures. As a result, stipulated oil change intervals must be strictly observed.
Sealing
The bearings are of an open design
Four point contact bearings are supplied without seals. As a result, sealing of the bearing position must be carried out in the adjacent construction. The sealing system should reliably prevent:
- moisture and contaminants from entering the bearing
- the egress of lubricant from the bearing.
Speeds
Higher speeds are only possible under purely axial load
Due to the four point contact and resulting higher level of friction, the speed suitability of the bearings is heavily restricted under radial load. High speeds can only be achieved if four point contact ball bearings are subjected to purely axial load.
Limiting speeds and reference speeds in the product tables
Two speeds are generally indicated in the product tables ➤ dimension table:
- the kinematic limiting speed nG
- the thermal speed rating nϑr.
Limiting speed
The limiting speed nG is the kinematically permissible speed of a bearing. Even under favourable mounting and operating conditions, this value should not be exceeded without prior consultation with Schaeffler ➤ link. The values in the product tables are valid for oil lubrication.
Values for grease lubrication
For grease lubrication, 75% of the value stated in the product tables is permissible in each case.
Reference speeds
nϑr is used to calculate nϑ
The thermal speed rating nϑr is not an application-oriented speed limit, but is a calculated ancillary value for determining the thermally safe operating speed nϑ ➤ link.
Noise
The Schaeffler Noise Index (SGI) has been developed as a new feature for comparing the noise level of different bearing types and series. As a result, a noise evaluation of rolling bearings can now be carried out for the first time.
Schaeffler Noise Index
The SGI value is based on the maximum permissible noise level of a bearing in accordance with internal standards, which is calculated on the basis of ISO 15242. In order that different bearing types and series can be compared, the SGI value is plotted against the basic static load rating C0.
This permits direct comparisons between bearings with the same load carrying capacity. The upper limit value is given in each of the diagrams. This means that the average noise level of the bearings is lower than illustrated in the diagram.
The Schaeffler Noise Index is an additional performance characteristic in the selection of bearings for noise-sensitive applications. The specific suitability of a bearing for an application in terms of installation space, load carrying capacity or speed limit for example, must be checked independently of this.
Schaeffler Noise Index for four point contact bearings SGI = Schaeffler Noise Index C0 = basic static load rating |
![]() |
Temperature range
Limiting values
The operating temperature of the bearings is limited by:
- the dimensional stability of the bearing rings and rolling elements
- the cage
- the lubricant.
Possible operating temperatures for four point contact bearings ➤ Table .
Permissible temperature ranges
Operating temperature |
Four point contact bearing |
|
---|---|---|
with brass cage |
with polyamide cage PA66 |
|
|
–30 °C to +150 °C, |
–30 °C to +120 °C |
In the event of anticipated temperatures which lie outside the stated values, please contact Schaeffler.
Cages
Solid cages made from brass and polyamide PA66 are used as standard
Standard cages and additional designs for four point contact bearings ➤ Table . Other cage designs are available by agreement. With such cages, however, suitability for high speeds and temperatures as well as the basic load ratings may differ from the values for the bearings with standard cages.
For high continuous temperatures and applications with difficult operating conditions, bearings with brass or sheet steel cages should be used. If there is any uncertainty regarding cage suitability, please consult Schaeffler.
Cage, cage suffix, bore code
Bearing series |
Solid brass cage |
Solid cage |
||
---|---|---|---|---|
MPA |
TVP |
|||
standard |
also available for |
standard |
also available for |
|
Bore code |
||||
QJ10 |
12, 17, 19, 21, 22, 24, 26, 30 to 40 |
‒ |
‒ |
‒ |
QJ2 |
up to 08, 10, 13, |
09, 11, 12, 14, 15, 18 |
09, 11,12, 14, 15, 18 |
08 |
QJ3 |
03, 04, from 10 |
05 to 09 |
05 to 09 |
‒ |
Internal clearance
Axial internal clearance
The standard is CN
Four point contact bearings are manufactured as standard with axial internal clearance CN (normal) ➤ Table. CN is not stated in the designation.
Certain sizes are also available by agreement with the smaller internal clearance C2 and with the larger internal clearance C3 and C4.
The values for axial internal clearance correspond to DIN 628-4:2008 (ISO 5753-2:2010) ➤ Table. They are valid for bearings which are free from load and measurement forces (without elastic deformation).
Axial internal clearance of four point contact bearings
Nominal |
Axial internal clearance |
||||||||
---|---|---|---|---|---|---|---|---|---|
d mm |
C2 μm |
CN μm |
C3 μm |
C4 μm |
|||||
over |
incl. |
min. |
max. |
min. |
max. |
min. |
max. |
min. |
max. |
10 |
18 |
15 |
65 |
50 |
95 |
85 |
130 |
120 |
165 |
18 |
40 |
25 |
75 |
65 |
110 |
100 |
150 |
135 |
185 |
40 |
60 |
35 |
85 |
75 |
125 |
110 |
165 |
150 |
200 |
60 |
80 |
45 |
100 |
85 |
140 |
125 |
175 |
165 |
215 |
80 |
100 |
55 |
110 |
95 |
150 |
135 |
190 |
180 |
235 |
100 |
140 |
70 |
130 |
115 |
175 |
160 |
220 |
205 |
265 |
140 |
180 |
90 |
155 |
135 |
200 |
185 |
250 |
235 |
300 |
180 |
220 |
105 |
175 |
155 |
225 |
210 |
280 |
260 |
330 |
Dimensions, tolerances
Dimension standards
The main dimensions of four point contact bearings correspond to DIN 628-4:2008. Nominal dimensions of four point contact bearings ➤ dimension table.
Chamfer dimensions
The limiting dimensions for chamfer dimensions correspond to DIN 620‑6:2004. Overview and limiting values ➤ section. Nominal value of chamfer dimension ➤ dimension table.
Tolerances
The tolerances for the dimensional and running accuracy of four point contact bearings correspond to tolerance class Normal in accordance with ISO 492:2014. Tolerance values in accordance with ISO 492 ➤ Table.
Retaining slots
The dimensions and tolerances of the retaining slots correspond to ISO 20515:2012 and DIN 628-4:2008.
Suffixes
For a description of the suffixes used in this chapter see ➤ Table and medias interchange http://www.schaeffler.de/std/1B69 .
Suffixes and corresponding descriptions
Suffix |
Description of suffix |
|
---|---|---|
C2 |
Axial internal clearance C2 |
Special design, |
C3 |
Axial internal clearance C3 |
|
C4 |
Axial internal clearance C4 |
|
MPA |
Solid brass cage, guided on outer ring |
Standard, |
TVP |
Solid cage made from |
|
XL |
X-life bearing |
Standard, |
N2 |
Two retaining slots in outer ring |
Standard for larger bearings |
Structure of bearing designation
Example of composition of bearing designation
The designation of bearings follows a set model. For an example of this see ➤ Figure . The composition of designations is subject to DIN 623-1 ➤ Figure.
Four point contact bearing with two retaining slots in the outer ring: designation structure |
![]() |
Dimensioning
Equivalent dynamic bearing load
P = Fr under purely radial load of constant magnitude and direction
The basic rating life equation L = (Cr/P)p used in the dimensioning of bearings under dynamic load assumes a load of constant magnitude and direction. In radial bearings, this is a purely radial load Fr. If this condition is met, the bearing load Fr is used in the rating life equation for P (P = Fr).
P is a substitute force for combined load and various load cases
If this condition is not met, a constant radial force must first be determined for the rating life calculation that (in relation to the rating life) represents an equivalent load. This force is known as the equivalent dynamic bearing load P.
Fa/Fr ≦ 0,95 or Fa/Fr > 0,95
The calculation of P is dependent on the load ratio Fa/Fr and the factor 0,95 ➤ Equation and ➤ Equation.
Equivalent dynamic load

Equivalent dynamic load

Legend
P | N |
Equivalent dynamic bearing load |
Fr | N |
Radial load |
Fa | N |
Axial load. |
Equivalent static bearing load
For four point contact bearings under static loading ➤ Equation .
Equivalent static load

Legend
P0 | N |
Equivalent static bearing load |
F0r, F0a | N |
Largest radial or axial load present (maximum load). |
Static load safety factor
S0 = C0/P0
In addition to the basic rating life L (L10h), it is also always necessary to check the static load safety factor S0 ➤ Equation.
Static load safety factor
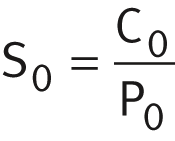
Legend
S0 |
Static load safety factor |
|
C0 | N |
Basic static load rating |
P0 | N |
Equivalent static bearing load. |
Minimum load
In order to prevent damage due to slippage, a minimum axial load of Fa ≧ 1,2 · Fr is required
In order to ensure low friction in the bearing, especially at high speeds, a minimum axial load is required. In order to prevent an excessive increase in friction in the bearing, the axial force should be sufficiently high that the rolling elements are in contact with the inner and outer ring raceway at only one point. This is ensured if Fa ≧ 1,2 · Fr.
Design of bearing arrangements
When used as axial bearings, the outer ring must be radially relieved in the housing
If a four point contact bearing is used as a pure axial bearing, the outer ring must have a large radial clearance in the housing, in order that the bearing is not subjected to radial load ➤ Figure.
Support bearing rings over their entire circumference and width
In order to allow full utilisation of the load carrying capacity of the bearings and thus also achieve the requisite rating life, the bearing rings must be rigidly and uniformly supported by means of contact surfaces over their entire circumference and over the entire width of the raceway (not applicable to bearings with radially relieved outer rings). The seating and contact surfaces should not be interrupted by grooves, holes or other recesses. The accuracy of mating parts must meet specific requirements ➤ Table to ➤ Table.
Radial location of bearings – fit recommendations
For secure radial location, tight fits are necessary
In addition to supporting the rings adequately, the bearings must also be securely located in a radial direction, to prevent creep of the bearing rings on the mating parts under load. This is generally achieved by means of tight fits between the bearing rings and the mating parts. If the rings are not secured adequately or correctly, this can cause severe damage to the bearings and adjacent machine parts. Influencing factors, such as the conditions of rotation, magnitude of the load, internal clearance, temperature conditions, design of the mating parts and the mounting and dismounting options must be taken into consideration in the selection of fits.
If shock type loads occur, tight fits (transition fit or interference fit) are required to prevent the rings from coming loose at any point. Clearance, transition or interference fits ➤ Table and ➤ Table.
The following information provided in Technical principles must be taken into consideration in the design of bearing arrangements:
Location of the outer ring by means of retaining slots
For location of the bearings in the housing by means of retaining slots and locking pin ➤ Figure .
Axial location of bearings – location methods
The bearings must also be securely located in an axial direction
As a tight fit alone is not normally sufficient to also locate the bearing rings securely on the shaft and in the housing bore in an axial direction, this must usually be achieved by means of an additional axial location or retention method. The axial location of the bearing rings must be matched to the type of bearing arrangement. Shaft and housing shoulders, housing covers, nuts, spacer rings and retaining rings etc., are fundamentally suitable ➤ Figure.
Dimensional, geometrical and running accuracy of the bearing seats
A minimum of IT6 should be provided for the shaft seat and a minimum of IT7 for the housing seat
The accuracy of the bearing seat on the shaft and in the housing should correspond to the accuracy of the bearing used. For four point contact bearings with the tolerance class Normal, the shaft seat should correspond to a minimum of standard tolerance grade IT6 and the housing seat to a minimum of IT7. Guide values for the geometrical and positional tolerances of bearing seating surfaces ➤ Table, tolerances t1 to t3 in accordance with ➤ Figure. Numerical values for IT grades ➤ Table.
Guide values for the geometrical and positional tolerances of bearing seating surfaces
Bearing |
Bearing seating surface |
Standard tolerance grades to ISO 286-1 |
||||
---|---|---|---|---|---|---|
to ISO 492 |
to DIN 620 |
Diameter tolerance |
Roundness tolerance |
Parallelism tolerance |
Total axial runout tolerance |
|
t1 |
t2 |
t3 |
||||
Normal |
PN (P0) |
Shaft |
IT6 (IT5) |
Circumferential load IT4/2 |
Circumferential load IT4/2 |
IT4 |
Point load IT5/2 |
Point load IT5/2 |
|||||
Housing |
IT7 (IT6) |
Circumferential load IT5/2 |
Circumferential load IT5/2 |
IT5 |
||
Point load IT6/2 |
Point load IT6/2 |
Numerical values for ISO standard tolerances (IT grades) to ISO 286-1:2010
IT grade |
Nominal dimension in mm |
||||||||
---|---|---|---|---|---|---|---|---|---|
over |
10 |
18 |
30 |
50 |
80 |
120 |
180 |
250 |
|
incl. |
18 |
30 |
50 |
80 |
120 |
180 |
250 |
315 |
|
Values in μm |
|||||||||
IT4 |
5 |
6 |
7 |
8 |
10 |
12 |
14 |
16 |
|
IT5 |
8 |
9 |
11 |
13 |
15 |
18 |
20 |
23 |
|
IT6 |
11 |
13 |
16 |
19 |
22 |
25 |
29 |
32 |
|
IT7 |
18 |
21 |
25 |
30 |
35 |
40 |
46 |
52 |
Roughness of cylindrical bearing seating surfaces
Ra must not be too high
The roughness of the bearing seats must be matched to the tolerance class of the bearings. The mean roughness value Ra must not be too high, in order to maintain the interference loss within limits. The shafts must be ground, while the bores must be precision turned. Guide values as a function of the IT grade of bearing seating surfaces ➤ Table.
Roughness values for cylindrical bearing seating surfaces – guide values
Nominal diameter d (D) |
Recommended mean roughness value Ramax |
||||
---|---|---|---|---|---|
mm |
μm |
||||
Diameter tolerance (IT grade) |
|||||
over |
incl. |
IT7 |
IT6 |
IT5 |
IT4 |
‒ |
80 |
1,6 |
0,8 |
0,4 |
0,2 |
80 |
500 |
1,6 |
1,6 |
0,8 |
0,4 |
Mounting dimensions for the contact surfaces of bearing rings
The contact surfaces for the rings must be of sufficient height
The mounting dimensions of the shaft and housing shoulders, and spacer rings etc., must ensure that the contact surfaces for the bearing rings are of sufficient height. However, they must also reliably prevent rotating parts of the bearing from grazing stationary parts. Proven mounting dimensions for the radii and diameters of the abutment shoulders ➤ dimension table. These dimensions are limiting dimensions (maximum or minimum dimensions); the actual values should not be higher or lower than specified.
Mounting and dismounting
The mounting and dismounting options for four point contact bearings, by thermal, hydraulic or mechanical methods, must be taken into consideration in the design of the bearing position.
As the bearings are not self-retaining, they are easy to mount
Four point contact bearings are not self-retaining. As a result, the outer ring with the ball and cage assembly can be mounted separately from the two inner ring halves ➤ section. This gives simplified mounting of the bearings.
Schaeffler Mounting Handbook
Rolling bearings must be handled with great care
Rolling bearings are well-proven precision machine elements for the design of economical and reliable bearing arrangements, which offer high operational security. In order that these products can function correctly and achieve the envisaged operating life without detrimental effect, they must be handled with care.
The Schaeffler Mounting Handbook MH 1 gives comprehensive information about the correct storage, mounting, dismounting and maintenance of rotary rolling bearings http://www.schaeffler.de/std/1B68. It also provides information which should be observed by the designer, in relation to the mounting, dismounting and maintenance of bearings, in the original design of the bearing position. This book is available from Schaeffler on request.
Legal notice regarding datafreshness
The further development of products may also result in technical changes to catalogue products
Of central interest to Schaeffler is the further development and optimisation of its products and the satisfaction of its customers. In order that you, as the customer, can keep yourself optimally informed about the progress that is being made here and with regard to the current technical status of the products, we publish any product changes which differ from the printed version in our electronic product catalogue.
We therefore reserve the right to make changes to the data and illustrations in this catalogue. This catalogue reflects the status at the time of printing. More recent publications released by us (as printed or digital media) will automatically precede this catalogue if they involve the same subject. Therefore, please always use our electronic product catalogue to check whether more up-to-date information or modification notices exist for your desired product.
Further information
In addition to the data in this chapter, the following chapters in Technical principles must also be observed in the design of bearing arrangements: