Design of bearing arrangements
Arrangement of bearings
Support of a shaft normally requires two bearings
The guidance and support of a rotating machine part generally requires at least two bearings arranged at a certain distance from each other (exceptions: four point contact, crossed roller and slewing bearings). Depending on the application, a decision is made between a locating/non-locating bearing arrangement, an adjusted bearing arrangement and a floating bearing arrangement.
Locating/non-locating bearing arrangement
The non-locating bearing compensates for differences in distance
On a shaft supported by two radial bearings, the distances between the bearing seats on the shaft and in the housing frequently do not coincide as a result of manufacturing tolerances. The distances may also change as a result of temperature increases during operation. These differences in distance are compensated in the non-locating bearing. Examples of locating/non-locating bearing arrangements ➤ Figure.
Non-locating bearings
Suitable non-locating bearings
Ideal non-locating bearings are cylindrical roller bearings with cage of series N and NU or needle roller bearings. In these bearings, the roller and cage assembly can be displaced on the raceway of the bearing ring without ribs. All other bearing types, for example deep groove ball bearings and spherical roller bearings, can only act as non-locating bearings if one bearing ring has a fit that allows displacement. The bearing ring subjected to point load therefore has a loose fit; this is normally the outer ring.
Locating bearings
The locating bearing guides the shaft in an axial direction and supports external axial forces. In order to prevent axial bracing, shafts with more than two bearings have only one locating bearing. The type of bearing selected as a locating bearing depends on the magnitude of the axial forces and the accuracy with which the shafts must be axially guided.
Suitable locating bearings
A double row angular contact ball bearing, for example, will give closer axial guidance than a deep groove ball bearing or a spherical roller bearing. A pair of symmetrically arranged angular contact ball bearings or tapered roller bearings used as locating bearings will also provide extremely close axial guidance.
There are particular advantages in using angular contact ball bearings of the universal design. The bearings can be fitted in pairs in any O or X arrangement without shims. Angular contact ball bearings of the universal design are matched so that, in an X or O arrangement, they have a low axial internal clearance (design UA), zero clearance (UO) or slight preload (UL).
In gearboxes, a four point contact bearing is sometimes fitted directly adjacent to a cylindrical roller bearing to give a locating bearing arrangement. The four point contact bearing, without radial support of the outer ring, can only support axial forces. The radial force is supported by the cylindrical roller bearing.
If a lower axial force is present, a cylindrical roller bearing with cage of series NUP can also be used as a locating bearing.
No adjustment or setting work with matched pairs of tapered roller bearings
Fitting is also made easier when using matched pairs of tapered roller bearings as locating bearings (313..-N11CA). They are matched with appropriate axial internal clearance so that no adjustment or setting work is required.
Locating/non-locating bearing arrangements
|
![]() |
Adjusted bearing arrangement
The “adjustment” process
An adjusted bearing arrangement is generally constructed from two angular contact bearings (angular contact ball bearings, tapered roller bearings) in a mirror image arrangement ➤ Figure and ➤ Figure. The inner and outer rings of the bearings are displaced relative to each other until the required clearance or the required preload is achieved. This process is known as “adjustment”.
Angular contact bearings and deep groove ball bearings suitable for adjusted bearing arrangements
Angular contact bearings support radial and axial forces
Angular contact bearings support forces comprising a radial and an axial component. These are thus a combination of a radial and an axial bearing. Depending on the size of the nominal contact angle α, angular contact bearings are classified as radial or axial bearings.
Deep groove ball bearings are also suitable
Deep groove ball bearings can also be used for an adjusted bearing arrangement; these are then angular contact ball bearings with a small nominal contact angle.
Due to the possibility of regulating the clearance, adjusted bearing arrangements are particularly suitable if close guidance is necessary.
O or X arrangement
Two arrangements
In an adjusted bearing arrangement, an O or X arrangement of the bearings is essentially possible.
The contact cone apexes point outwards or inwards
In the O arrangement, the cones and their apexes formed by the contact lines (the contact cone apexes S) point outwards, in the X arrangement, the cones point inwards ➤ Figure.
In angular contact ball bearings and tapered roller bearings, the contact lines of the rolling element forces coincide at the contact cone apexes S ➤ Figure and ➤ Figure. In adjusted bearing arrangements, the bearing spacing is therefore defined as the spacing of the contact cone apexes.
The support spacing is larger in an O arrangement
The resulting support spacing H is larger in an O arrangement than in an X arrangement. An O arrangement should be used in preference if the component with small bearing spacing must be guided with the smallest possible tilting clearance or tilting forces must be supported.
Adjusted bearing arrangement with angular contact ball bearings S = contact cone apex H = support spacing
|
![]() |
Influence of thermal expansion in O and X arrangements
When deciding between an O and X arrangement, attention must also be paid to the temperature conditions and thermal expansions. This is based on the position of the roller cone apexes R. The roller cone apex R represents the intersection point of the extended, inclined outer ring raceway with the bearing axis ➤ Figure.
X arrangement
If the shaft is warmer than the housing (TW > TG ), the shaft expands more than the housing in an axial and radial direction. As a result, the clearance set in an X arrangement decreases in every case (assuming the following precondition: shaft and housing of same material).
Adjusted bearing arrangement with tapered roller bearings X arrangement R = roller cone apex S = contact cone apex |
![]() |
Temperature behaviour and thermal expansion in an O arrangement
The behaviour is different in an O arrangement. A distinction must be drawn between three cases here:
- If the roller cone apexes R coincide at a point, the axial and radial thermal expansion cancel each other out and the clearance set is maintained ➤ Figure
- If the roller cones overlap with a small bearing spacing, the radial expansion has a stronger effect than the axial expansion on the bearing clearance ➤ Figure: the axial clearance is reduced. This must be taken into consideration in the adjustment of bearings
- In the third case, the roller cones do not overlap with a large bearing spacing ➤ Figure. The radial expansion then has a weaker effect than the axial expansion on the bearing clearance: the axial clearance is increased
Adjusted bearings in an O arrangement, the roller cone apexes coincide R = roller cone apex S = contact cone apex |
![]() |
Adjusted bearings in an O arrangement, the roller cone apexes overlap R = roller cone apex S = contact cone apex |
![]() |
Adjusted bearings in an O arrangement, the roller cone apexes do not overlap R = roller cone apex S = contact cone apex |
![]() |
Sliding seat in the bearing ring to be adjusted
Sliding seat only permissible on the bearing ring with point load
Whether the inner ring or outer ring is adjusted depends on the degree of accessibility of the adjustment elements, such as nuts and covers. Since the bearing ring to be adjusted must be easily displaced, attention must also be paid in these considerations to the fits of the bearing rings.
A sliding seat should fundamentally only be permitted on the ring that is subject to point load.
Elastic adjustment
Preloading using springs
Adjusted bearing arrangements can also be achieved by preloading using springs ➤ Figure. This elastic adjustment method compensates for thermal expansion. It can also be used where bearing arrangements are at risk of vibration while stationary.
Bearing arrangement adjusted by means of spring washer
|
![]() |
Floating bearing arrangement
Difference from the adjusted bearing arrangement: this does not give close axial guidance
The floating bearing arrangement is essentially similar in its arrangement to the adjusted bearing arrangement. While freedom from clearance or even preload is desirable when warm from operation in the latter case, floating bearing arrangements always have an axial clearance s of several tenths of a millimetre depending on the bearing size ➤ Figure. The value s is defined as a function of the required guidance accuracy such that the bearings are not axially stressed even under unfavourable thermal conditions.
Suitable bearing types
A floating bearing arrangement is suitable for bearings that must not be adjusted
For a floating bearing arrangement, almost all bearing types can be considered that must not be adjusted; examples ➤ Figure. Floating arrangements are thus possible with, for example, deep groove ball bearings, self-aligning ball bearings and spherical roller bearings; one ring of each of the two bearings (usually the outer ring) then has a sliding seat. In the floating bearing arrangement with cylindrical roller bearings NJ, length compensation is possible within the bearing.
Tapered roller bearings and angular contact ball bearings are not suitable for a floating bearing arrangement, since these bearings must be adjusted in order to run correctly.
Floating bearing arrangements s = axial displacement distance (axial clearance)
|
![]() |
Radial location of bearings
Location of the bearing rings in a radial and tangential direction by fit, in an axial direction by form fit
Rolling bearings must be located on the shaft and in the housing in a radial, axial and tangential direction in accordance with their function. In a radial and tangential direction, this occurs by means of a tight fit. However, this is only possible under certain conditions in an axial direction, therefore rolling bearings are generally axially located by means of form fit.
Criteria for selection of fits
Points to be observed in the selection of fits
The following must be taken into consideration in determining the fit:
- The rolling bearing rings must be well supported over their entire circumference in order to allow full utilisation of the load carrying capacity of the bearing
- The rings must not creep on their mating parts, otherwise the seating surfaces will be damaged
- The non-locating bearing must compensate changes in the length of the shaft and housing and one ring must therefore be axially adjustable
- Mounting and dismounting of the bearings should be possible without a large amount of work
Interference fits
Interference fits lead to expansion of the inner ring raceway and contraction of the outer ring raceway. The resulting stresses occurring in the rings and the reduction in the radial internal clearance must be taken into consideration in the selection of the fit; see ➤ link and ➤ link.
Tight fit necessary
Good support of the bearing rings on their circumference requires rigid seating. The requirement that rings must not creep on their mating parts also requires firm seating. If non-separable bearings must be mounted and dismounted, a tight fit can only be achieved for one bearing ring. In the case of cylindrical roller bearings N, NU and needle roller bearings, both rings can have tight fits, since the length compensation takes place within the bearing and since the rings can be mounted separately. With tight fits and a temperature differential between the inner and outer ring, the radial internal clearance of the bearing is reduced. This must be taken into consideration when selecting the radial internal clearance.
Materials other than cast iron or steel
If materials other than cast iron or steel are used for the adjacent construction, the modulus of elasticity and the differing coefficients of thermal expansion of the materials must also be be taken into consideration to achieve rigid seating. For aluminium housings, thin-walled housings and hollow shafts, a closer fit should be selected if necessary in order to achieve the same force locking as with cast iron, steel or solid shafts.
Higher loads
Higher loads, especially shocks, require a fit with larger interference and narrower geometrical tolerances.
Bearing seat for axial bearings
Axial bearings, which support axial loads only, must not be guided radially (with the exception of axial cylindrical roller bearings which have a degree of freedom in the radial direction due to flat raceways). In the case of groove-shaped raceways this is not present and must be achieved by a loose seat for the stationary washer. A rigid seat is normally selected for the rotating washer.
Where axial bearings also support radial forces, such as in axial spherical roller bearings, fits should be selected in the same way as for radial bearings.
Contact surfaces of the mating parts
The contact surfaces of the mating parts must be perpendicular to the axis of rotation (total axial runout tolerance to IT5 or better), in order to ensure uniform load distribution over all the rolling elements.
Conditions of rotation
Point or circumferential load
The conditions of rotation indicate the motion of one bearing ring with respect to the load direction and are expressed as either circumferential load or point load ➤ Table.
For point load, a loose fit is also possible
If the bearing ring is stationary relative to the load direction (point load on the ring), no forces occur that could cause creep of the ring. A tight fit would be desirable here in order to give better support, but a loose fit is also possible since there is no risk that the ring will undergo creep. There is essentially a risk, however, that fretting corrosion will occur.
For circumferential load, a firm bearing seat is necessary
A bearing ring that rotates relative to the load direction (circumferential load on the ring) will roll on its seat if a loose fit is present and will thus creep in a circumferential direction. If shock type load is present, the ring will slip. In both cases, there is a risk that the seats of the ring and mating part will be damaged by fretting corrosion and wear.
The possible creep or slippage of a bearing ring can only be effectively prevented by a firm bearing seat.
Differentiation between point load and circumferential load
Condition of rotation |
Example |
Schematic |
Load case |
Fit |
---|---|---|---|---|
Rotating inner ring, stationary outer ring |
Shaft with weight load |
![]() |
Circumferential load |
Inner ring: Outer ring: |
Constant load direction |
Shaft with weight load | |||
Stationary inner ring, rotating outer ring |
Hub bearing arrangement with significant imbalance |
![]() |
Circumferential load on inner ring and point load on outer ring |
Inner ring: Outer ring: |
Load direction rotates with outer ring |
Hub bearing arrangement with significant imbalance | |||
Stationary inner ring, rotating outer ring |
Passenger car front wheel track roller (hub bearing arrangement) |
![]() |
Point load on inner ring and circumferential load |
Inner ring: Outer ring: |
Constant load direction |
Passenger car front wheel track roller (hub bearing arrangement) | |||
Rotating inner ring, stationary outer ring |
Centrifuge, vibrating screen |
![]() |
Point load on inner ring and circumferential load on outer ring |
Inner ring: Outer ring: |
Load direction rotates with inner ring |
Centrifuge, vibrating screen |
Recommended fits
Shaft and housing tolerances
ISO tolerance classes
The tolerances are defined in the form of ISO tolerance classes to ISO 286‑1 and ISO 286-2. The designation of the tolerance classes, e. g. “E8”, comprises one or two upper case letters for housings or lower case letters for shafts (= fundamental deviation identifier, which defines the tolerance position relative to the zero line, e. g. “E”) and the grade number of the standard tolerance grade (this defines the tolerance quality, e. g. “8”). A schematic illustration of the most common rolling bearing fits is shown in ➤ Figure.
Shaft and housing fits for rolling bearings D = nominal bearing outside diameter d = nominal bearing bore diameter tΔDmp = deviation of mean bearing outside diameter (in accordance with ISO 492) tΔdmp = deviation of mean bearing bore diameter (in accordance with ISO 492)
|
![]() |
Recommendations for shaft and housing tolerances
The tables ➤ Table to ➤ Table contain recommendations for the selection of shaft and housing tolerances that are valid for normal mounting and operating conditions. Deviations are possible if particular requirements apply, for example in relation to running accuracy, smooth running or operating temperature. Increased running accuracies thus require closer tolerances such as standard tolerance grade 5 instead of 6. If the inner ring is warmer than the shaft during operation, the seating may loosen to an impermissible extent. A tighter fit must then be selected, for example m6 instead of k6.
Objective: the best overall solution
In some applications, the question of fits can only be resolved by a compromise. The individual requirements must be weighed against each other and those selected that give the best overall solution.
Tolerance classes for cylindrical shaft seats (radial bearings)
Condition |
Bearing type |
Shaft diameter |
Displacement facility Load |
Tolerance class2) |
||
---|---|---|---|---|---|---|
mm |
||||||
over |
incl. |
|||||
Point load on inner ring | ||||||
Ball bearings, roller bearings |
All sizes |
Inner ring easily displaced |
g6 (g5) |
|||
Ball bearings, roller bearings | All sizes |
Inner ring not easily displaced, angular contact ball bearings and tapered roller bearings with adjusted inner ring |
h6 (j6) |
|||
Needle |
All sizes |
Non-locating bearing |
h6 (g6)3) |
|||
Circumferential load on inner ring or indeterminate load direction |
||||||
Ball bearings | ||||||
‒ |
50 |
Normal loads4) |
j6 (j5) |
|||
50 |
100 |
Low loads5) |
j6 (j5) |
|||
50 | 100 |
Normal and high loads6) |
k6 (k5) |
|||
100 |
200 |
Low loads4) |
k6 (m6) |
|||
100 | 200 |
Normal and high loads7) |
m6 (m5) |
|||
200 |
‒ |
Low loads |
m6 (m5) |
|||
200 | ‒ |
Normal and high loads |
n6 (n5) |
|||
Roller bearings | ||||||
‒ |
60 |
Low loads |
j6 (j5) |
|||
‒ | 60 | Normal and high loads | k6 (k5) | |||
60 | 200 | Low loads | k6 (k5) | |||
60 | 200 | Normal loads | m6 (m5) | |||
60 | 200 | High loads | n6 (n5) | |||
200 | 500 | Normal loads | m6 (n6) | |||
200 | 500 | High loads, shocks | p6 | |||
500 | ‒ | Normal loads | n6 (p6) | |||
500 | ‒ | High loads | p6 | |||
Needle roller bearings | ||||||
‒ |
50 |
Low loads |
k6 |
|||
‒ | 50 | Normal and high loads | m6 | |||
50 | 120 | Low loads | m6 | |||
50 | 120 | Normal and high loads | n6 | |||
120 |
250 |
Low loads |
n6 |
|||
120 | 250 |
Normal and high loads |
p6 |
|||
250 |
400 |
Low loads |
p6 |
|||
250 | 400 |
Normal and high loads |
r6 |
|||
400 |
500 |
Low loads |
r6 |
|||
400 | 500 |
Normal and high loads |
s6 |
|||
500 | ‒ | Low loads | r6 | |||
500 | ‒ | Normal and high loads | s6 |
- Condition of rotation ➤ Table.
- The envelope requirement Ⓔ ➤ Figure applies.
- For easy fitting.
- C0/P > 10.
- C0/P > 12.
- C0/P < 12.
- C0/P < 10.
Tolerance classes for cylindrical shaft seats (axial bearings)
Load |
Bearing type |
Shaft diameter |
Operating conditions |
Tolerance class1) |
|
---|---|---|---|---|---|
mm |
|||||
over |
incl. |
||||
Axial load | |||||
Axial deep groove ball bearings |
All sizes |
– |
j6 | ||
Axial deep groove ball bearings, double direction |
All sizes |
– |
k6 | ||
Axial cylindrical roller bearings with shaft locating washer |
All sizes |
– |
h8 |
||
Axial cylindrical roller and cage assemblies |
All sizes |
– |
h8 | ||
Combined load | |||||
Axial spherical roller bearings |
All sizes |
Point load on shaft locating washer |
j6 | ||
Axial spherical roller bearings |
‒ |
200 |
Circumferential load on shaft locating washer |
j6 (k6) |
|
Axial spherical roller bearings |
200 |
‒ |
Circumferential load on shaft locating washer |
k6 (m6) |
- The envelope requirement Ⓔ ➤ Figure applies.
Tolerance classes for bearing seats in housings (radial bearings)
Condition |
Displacement facility Load |
Operating conditions |
Tolerance class2) |
---|---|---|---|
Point load on outer ring | |||
Outer ring easily displaced, housing unsplit |
The tolerance grade |
H7 (H6)3) |
|
Outer ring easily displaced, housing split |
The tolerance grade is determined by the running accuracy required |
H8 (H7) |
|
Outer ring not easily displaced, housing unsplit |
High running accuracy required |
H6 (J6) |
|
Outer ring not easily displaced, angular contact ball bearings and tapered roller bearings with adjusted outer ring, housing split |
Normal running accuracy |
H7 (J7) |
|
Outer ring easily displaced |
Heat input via shaft |
G74) | |
Circumferential load on outer ring or indeterminate load direction | |||
Low loads, outer ring cannot be displaced |
High requirements |
K7 (K6) |
|
Normal loads, shocks, outer ring cannot be displaced |
High requirements for running accuracy: K6, M6, N6 and P6 |
M7 (M6) |
|
High loads, shocks (C0/P < 6), outer ring cannot be displaced |
High requirements for running accuracy: K6, M6, N6 and P6 |
N7 (N6) |
|
High loads, severe shocks, thin‑walled housing, outer ring cannot be displaced |
High requirements for running accuracy: K6, M6, N6 and P6 |
P7 (P6) |
- Condition of rotation ➤ Table.
- The envelope requirement Ⓔ ➤ Figure applies.
- G7 for housings made from flake graphite cast iron, with bearing outside diameter D > 250 mm and temperature differential between outer ring and housing > 10 K.
- F7 for housings made from flake graphite cast iron, with bearing outside diameter D > 250 mm and temperature differential between outer ring and housing > 10 K.
Tolerance classes for bearing seats in housings (axial bearings)
Load |
Bearing type |
Operating conditions |
Tolerance class1) |
---|---|---|---|
Axial load | |||
Axial deep groove ball bearings |
Normal running accuracy |
E8 |
|
Axial deep groove ball bearings |
High running accuracy |
H6 |
|
Axial cylindrical roller bearings with housing locating washer |
‒ |
H9 |
|
Axial cylindrical roller and cage assemblies |
‒ |
H10 | |
Axial spherical roller bearings |
Normal loads |
E8 |
|
Axial spherical roller bearings |
High loads |
G7 |
|
Combined loads, point load on housing locating washer |
|||
Axial spherical roller bearings |
‒ |
H7 | |
Combined loads, circumferential load on housing locating washer |
|||
Axial spherical roller bearings |
‒ |
K7 |
- The envelope requirement Ⓔ ➤ Figure applies.
Tables of fits
Clearance, transition and interference fits for shafts and housing bores
Machining tolerances for shafts and housing bores are shown in ➤ Figure, ➤ Table and ➤ Table. The values are valid for solid steel shafts and flake graphite cast iron housings. In the table header, below the nominal diameters, are the normal tolerances for the bore or outside diameter of radial bearings (excluding tapered roller bearings). Below these are the deviations for the most important tolerance classes for mounting of rolling bearings.
Example for shaft fit, tolerance class j5
For the shaft ⌀ 40 j5 Ⓔ, ➤ Table gives an example of how to read the numerical values.
Example for housing fit, tolerance class K6
For the housing bore ⌀ 100 K6 Ⓔ, ➤ Table gives an example explaining the group of numbers.
Shaft fits
Nominal shaft diameter in mm |
|||||||||||||||||||||||||||||||||||||||||||||||||||||||||
---|---|---|---|---|---|---|---|---|---|---|---|---|---|---|---|---|---|---|---|---|---|---|---|---|---|---|---|---|---|---|---|---|---|---|---|---|---|---|---|---|---|---|---|---|---|---|---|---|---|---|---|---|---|---|---|---|---|
over incl. |
3 6 |
6 10 |
10 18 |
18 30 |
30 50 |
50 65 |
over incl. |
65 80 |
80 100 |
100 120 |
120 140 |
140 160 |
over incl. |
160 180 |
180 200 |
200 220 |
220 250 |
250 280 |
over incl. |
280 315 |
315 355 |
355 400 |
400 450 |
450 500 |
over incl. |
500 560 |
560 630 |
630 710 |
710 800 |
800 900 |
over incl. |
||||||||||||||||||||||||||
Deviations of bearing bore diameter in μm (tolerance class Normal) |
|||||||||||||||||||||||||||||||||||||||||||||||||||||||||
tΔdmp |
0 –8 |
0 –8 |
0 –8 |
0 –10 |
0 –12 |
0 –15 |
tΔdmp |
0 –15 |
0 –20 |
0 –20 |
0 –25 |
0 –25 |
tΔdmp |
0 –25 |
0 –30 |
0 –30 |
0 –30 |
0 –35 |
tΔdmp |
0 –35 |
0 –40 |
0 –40 |
0 –45 |
0 –45 |
tΔdmp |
0 –50 |
0 –50 |
0 –75 |
0 –75 |
0 –100 |
tΔdmp |
||||||||||||||||||||||||||
Shaft deviation, fit interference or fit clearance in μm |
|||||||||||||||||||||||||||||||||||||||||||||||||||||||||
f6 |
–10 –18 |
2 7 18 |
–13 –22 |
5 11 22 |
–16 –27 |
8 15 27 |
–20 –33 |
10 17 33 |
–25 –41 |
13 22 41 |
–30 –49 |
15 26 49 |
f6 |
–30 –49 |
15 26 49 |
–36 –58 |
16 30 58 |
–36 –58 |
16 30 58 |
–43 –68 |
18 34 68 |
–43 –68 |
18 34 68 |
f6 |
–43 –68 |
18 34 68 |
–50 –79 |
20 40 79 |
–50 –79 |
20 40 79 |
–50 –79 |
20 40 79 |
–56 –88 |
21 44 88 |
f6 |
–56 –88 |
21 44 88 |
–62 –98 |
22 47 98 |
–62 –98 |
22 47 98 |
–68 –108 |
23 51 108 |
–68 –108 |
23 51 108 |
f6 |
–76 –120 |
26 58 120 |
–76 –120 |
26 58 120 |
–80 –130 |
5 47 130 |
–80 –130 |
5 47 130 |
–86 –146 |
14 39 146 |
f6 |
g5 |
–4 –9 |
4 0 9 |
–5 –11 |
3 2 11 |
–6 –14 |
2 3 14 |
–7 –16 |
3 3 16 |
–9 –20 |
3 5 20 |
–10 –23 |
5 4 23 |
g5 |
–10 –23 |
5 4 23 |
–12 –27 |
8 4 27 |
–12 –27 |
8 4 27 |
–14 –32 |
11 3 32 |
–14 –32 |
11 3 32 |
g5 |
–14 –32 |
11 3 32 |
–15 –35 |
15 2 35 |
–15 –35 |
15 2 35 |
–15 –35 |
15 2 35 |
–17 –40 |
18 1 40 |
g5 |
–17 –40 |
18 1 40 |
–18 –43 |
22 0 43 |
–18 –43 |
22 0 43 |
–20 –47 |
25 1 47 |
–20 –47 |
25 1 47 |
g5 |
‒ |
‒ |
‒ |
‒ |
‒ |
‒ |
‒ |
‒ |
‒ |
‒ |
g5 |
g6 |
–4 –12 |
4 1 12 |
–5 –14 |
3 3 14 |
–6 –17 |
2 4 17 |
–7 –20 |
3 5 20 |
–9 –25 |
3 6 25 |
–10 –29 |
5 6 29 |
g6 |
–10 –29 |
5 6 29 |
–12 –34 |
8 6 34 |
–12 –34 |
8 6 34 |
–14 –39 |
11 6 39 |
–14 –39 |
11 6 39 |
g6 |
–14 –39 |
11 6 39 |
–15 –44 |
15 5 44 |
–15 –44 |
15 5 44 |
–15 –44 |
15 5 44 |
–17 –49 |
18 4 49 |
g6 |
–17 –49 |
18 4 49 |
–18 –54 |
22 3 54 |
–18 –54 |
22 3 54 |
–20 –60 |
25 3 60 |
–20 –60 |
25 3 60 |
g6 |
–22 –66 |
28 4 66 |
–22 –66 |
28 4 66 |
–24 –74 |
51 9 74 |
–24 –74 |
51 9 74 |
–26 –82 |
74 24 82 |
g6 |
h5 |
0 –5 |
8 4 5 |
0 –6 |
8 3 6 |
0 –8 |
8 3 8 |
0 –9 |
10 4 9 |
0 –11 |
12 4 11 |
0 –13 |
15 6 13 |
h5 |
0 –13 |
15 6 13 |
0 –15 |
20 8 15 |
0 –15 |
20 8 15 |
0 –18 |
25 11 18 |
0 –18 |
25 11 18 |
h5 |
0 –18 |
25 11 18 |
0 –20 |
30 13 20 |
0 –20 |
30 13 20 |
0 –20 |
30 13 20 |
0 –23 |
35 16 23 |
h5 |
0 –23 |
35 16 23 |
0 –25 |
40 18 25 |
0 –25 |
40 18 25 |
0 –27 |
45 21 27 |
0 –27 |
45 21 27 |
h5 |
0 –32 |
50 23 32 |
0 –32 |
50 23 32 |
0 –36 |
75 38 36 |
0 –36 |
75 38 36 |
0 –40 |
100 53 40 |
h5 |
h6 |
0 –8 |
8 3 8 |
0 –9 |
8 2 9 |
0 –11 |
8 2 11 |
0 –13 |
10 2 13 |
0 –16 |
12 3 16 |
0 –19 |
15 4 19 |
h6 |
0 –19 |
15 4 19 |
0 –22 |
20 6 22 |
0 –22 |
20 6 22 |
0 –25 |
25 8 25 |
0 –25 |
25 8 25 |
h6 |
0 –25 |
25 8 25 |
0 –29 |
30 10 29 |
0 –29 |
30 10 29 |
0 –29 |
30 10 29 |
0 –32 |
35 13 32 |
h6 |
0 –32 |
35 13 32 |
0 –36 |
40 15 36 |
0 –36 |
40 15 36 |
0 –40 |
45 17 40 |
0 –40 |
45 17 40 |
h6 |
0 –44 |
50 18 44 |
0 –44 |
50 18 44 |
0 –50 |
75 33 50 |
0 –50 |
75 33 50 |
0 –56 |
100 48 56 |
h6 |
Nominal shaft diameter in mm |
|||||||||||||||||||||||||||||||||||||||||||||||||||||||||
over incl. |
3 6 |
6 10 |
10 18 |
18 30 |
30 50 |
50 65 |
over incl. |
65 80 |
80 100 |
100 120 |
120 140 |
140 160 |
over incl. |
160 180 |
180 200 |
200 220 |
220 250 |
250 280 |
over incl. |
280 315 |
315 355 |
355 400 |
400 450 |
450 500 |
over incl. |
500 560 |
560 630 |
630 710 |
710 800 |
800 900 |
over incl. |
||||||||||||||||||||||||||
Deviations of bearing bore diameter in μm (tolerance class Normal) |
|||||||||||||||||||||||||||||||||||||||||||||||||||||||||
tΔdmp |
0 –8 |
0 –8 |
0 –8 |
0 –10 |
0 –12 |
0 –15 |
tΔdmp |
0 –15 |
0 –20 |
0 –20 |
0 –25 |
0 –25 |
tΔdmp |
0 –25 |
0 –30 |
0 –30 |
0 –30 |
0 –35 |
tΔdmp |
0 –35 |
0 –40 |
0 –40 |
0 –45 |
0 –45 |
tΔdmp |
0 –50 |
0 –50 |
0 –75 |
0 –75 |
0 –100 |
tΔdmp |
||||||||||||||||||||||||||
Shaft deviation, fit interference or fit clearance in μm |
|||||||||||||||||||||||||||||||||||||||||||||||||||||||||
j5 |
+3 –2 |
11 7 2 |
+4 –2 |
12 7 2 |
+5 –3 |
13 8 3 |
+5 –4 |
15 9 4 |
+6 –5 |
18 10 5 |
+6 –7 |
21 12 7 |
j5 |
+6 –7 |
21 12 7 |
+6 –9 |
26 14 9 |
+6 –9 |
26 14 9 |
+7 –11 |
32 18 11 |
+7 –11 |
32 18 11 |
j5 |
+7 –11 |
32 18 11 |
+7 –13 |
37 20 13 |
+7 –13 |
37 20 13 |
+7 –13 |
37 20 13 |
+7 –16 |
42 23 16 |
j5 |
+7 –16 |
42 23 16 |
+7 –18 |
47 25 18 |
+7 –18 |
47 25 18 |
+7 –20 |
52 28 20 |
+7 –20 |
52 28 20 |
j5 |
‒ |
‒ |
‒ |
‒ |
‒ |
‒ |
‒ |
‒ |
‒ |
‒ |
j5 |
j6 |
+6 –2 |
14 8 2 |
+7 –2 |
15 9 2 |
+8 –3 |
16 10 3 |
+9 –4 |
19 11 4 |
+11 –5 |
23 14 5 |
+12 –7 |
27 16 7 |
j6 |
+12 –7 |
27 16 7 |
+13 –9 |
33 19 9 |
+13 –9 |
33 19 9 |
+14 –11 |
39 22 11 |
+14 –11 |
39 22 11 |
j6 |
+14 –11 |
39 22 11 |
+16 –13 |
46 26 13 |
+16 –13 |
46 26 13 |
+16 –13 |
46 26 13 |
+16 –16 |
51 29 16 |
j6 |
+16 –16 |
51 29 16 |
+18 –18 |
58 33 18 |
+18 –18 |
58 33 18 |
+20 –20 |
65 37 20 |
+20 –20 |
65 37 20 |
j6 |
‒ |
‒ |
‒ |
‒ |
‒ |
‒ |
‒ |
‒ |
‒ |
‒ |
j6 |
js5 |
+2,5 –2,5 |
11 6 3 |
+3 –3 |
11 6 3 |
+4 –4 |
12 6 4 |
+4,5 –4,5 |
15 9 5 |
+5,5 –5,5 |
18 10 6 |
+6,5 –6,5 |
22 13 7 |
js5 |
+6,5 –6,5 |
22 13 7 |
+7,5 –7,5 |
28 16 8 |
+7,5 –7,5 |
28 16 8 |
+9 –9 |
34 20 9 |
+9 –9 |
34 20 9 |
js5 |
+9 –9 |
34 20 9 |
+10 –10 |
40 23 10 |
+10 –10 |
40 23 10 |
+10 –10 |
40 23 10 |
+11,5 –11,5 |
47 27 12 |
js5 |
+11,5 –11,5 |
47 27 12 |
+12,5 –12,5 |
53 32 13 |
+12,5 –12,5 |
53 32 13 |
+13,5 –13,5 |
59 35 14 |
+13,5 –13,5 |
59 35 14 |
js5 |
+16 –16 |
65 38 16 |
+16 –16 |
65 38 16 |
+18 –18 |
91 55 18 |
+18 –18 |
91 55 18 |
+20 –20 |
118 72 20 |
js5 |
js6 |
+4 –4 |
12 7 4 |
+4,5 –4,5 |
13 7 5 |
+5,5 –5,5 |
14 8 6 |
+6,5 –6,5 |
17 9 7 |
+8 –8 |
20 11 8 |
+9,5 –9,5 |
25 13 10 |
js6 |
+9,5 –9,5 |
25 13 10 |
+11 –11 |
31 17 11 |
+11 –11 |
31 17 11 |
+12,5 –12,5 |
38 21 13 |
+12,5 –12,5 |
38 21 13 |
js6 |
+12,5 –12,5 |
38 21 13 |
+14,5 –14,5 |
45 25 15 |
+14,5 –14,5 |
45 25 15 |
+14,5 –14,5 |
45 25 15 |
+16 –16 |
51 29 16 |
js6 |
+16 –16 |
51 29 16 |
+18 –18 |
58 33 18 |
+18 –18 |
58 33 18 |
+20 –20 |
65 37 20 |
+20 –20 |
65 37 20 |
js6 |
+22 –22 |
72 40 22 |
+22 –22 |
72 40 22 |
+25 –25 |
100 58 25 |
+25 –25 |
100 58 25 |
+28 –28 |
128 76 28 |
js6 |
k5 |
+6 +1 |
14 9 1 |
+7 +1 |
15 10 1 |
+9 +1 |
17 12 1 |
+11 +2 |
21 15 2 |
+13 +2 |
25 17 2 |
+15 +2 |
30 21 2 |
k5 |
+15 +2 |
30 21 2 |
+18 +3 |
38 26 3 |
+18 +3 |
38 26 3 |
+21 +3 |
46 32 3 |
+21 +3 |
46 32 3 |
k5 |
+21 +3 |
46 32 3 |
+24 +4 |
54 37 4 |
+24 +4 |
54 37 4 |
+24 +4 |
54 37 4 |
+27 +4 |
62 43 4 |
k5 |
+27 +4 |
62 43 4 |
+29 +4 |
69 47 4 |
+29 +4 |
69 47 4 |
+32 +5 |
77 53 5 |
+32 +5 |
77 53 5 |
k5 |
‒ |
‒ |
‒ |
‒ |
‒ |
‒ |
‒ |
‒ |
‒ |
‒ |
k5 |
k6 |
+9 +1 |
17 11 1 |
+10 +1 |
18 12 1 |
+12 +1 |
20 14 1 |
+15 +2 |
25 17 2 |
+18 +2 |
30 21 2 |
+21 +2 |
36 25 2 |
k6 |
+21 +2 |
36 25 2 |
+25 +3 |
45 31 3 |
+25 +3 |
45 31 3 |
+28 +3 |
53 36 3 |
+28 +3 |
53 36 3 |
k6 |
+28 +3 |
53 36 3 |
+33 +4 |
63 43 4 |
+33 +4 |
63 43 4 |
+33 +4 |
63 43 4 |
+36 +4 |
71 49 4 |
k6 |
+36 +4 |
71 49 4 |
+40 +4 |
80 55 4 |
+40 +4 |
80 55 4 |
+45 +5 |
90 62 5 |
+45 +5 |
90 62 5 |
k6 |
+44 0 |
94 62 0 |
+44 0 |
94 62 0 |
+50 0 |
125 83 0 |
+50 0 |
125 83 0 |
+56 0 |
156 104 0 |
k6 |
Nominal shaft diameter in mm |
|||||||||||||||||||||||||||||||||||||||||||||||||||||||||
over incl. |
3 6 |
6 10 |
10 18 |
18 30 |
30 50 |
50 65 |
over incl. |
65 80 |
80 100 |
100 120 |
120 140 |
140 160 |
over incl. |
160 180 |
180 200 |
200 220 |
220 250 |
250 280 |
over incl. |
280 315 |
315 355 |
355 400 |
400 450 |
450 500 |
over incl. |
500 560 |
560 630 |
630 710 |
710 800 |
800 900 |
over incl. |
||||||||||||||||||||||||||
Deviations of bearing bore diameter in μm (tolerance class Normal) |
|||||||||||||||||||||||||||||||||||||||||||||||||||||||||
tΔdmp |
0 –8 |
0 –8 |
0 –8 |
0 –10 |
0 –12 |
0 –15 |
tΔdmp |
0 –15 |
0 –20 |
0 –20 |
0 –25 |
0 –25 |
tΔdmp |
0 –25 |
0 –30 |
0 –30 |
0 –30 |
0 –35 |
tΔdmp |
0 –35 |
0 –40 |
0 –40 |
0 –45 |
0 –45 |
tΔdmp |
0 –50 |
0 –50 |
0 –75 |
0 –75 |
0 –100 |
tΔdmp |
||||||||||||||||||||||||||
Shaft deviation, fit interference or fit clearance in μm |
|||||||||||||||||||||||||||||||||||||||||||||||||||||||||
m5 |
+9 +4 |
17 13 4 |
+12 +6 |
20 15 6 |
+15 +7 |
23 18 7 |
+17 +8 |
27 21 8 |
+20 +9 |
32 24 9 |
+24 +11 |
39 30 11 |
m5 |
+24 +11 |
39 30 11 |
+28 +13 |
48 36 13 |
+28 +13 |
48 36 13 |
+33 +15 |
58 44 15 |
+33 +15 |
58 44 15 |
m5 |
+33 +15 |
58 44 15 |
+37 +17 |
67 50 17 |
+37 +17 |
67 50 17 |
+37 +17 |
67 50 17 |
+43 +20 |
78 59 20 |
m5 |
+43 +20 |
78 59 20 |
+46 +21 |
86 64 21 |
+46 +21 |
86 64 21 |
+50 +23 |
95 71 23 |
+50 +23 |
95 71 23 |
m5 |
‒ |
‒ |
‒ |
‒ |
‒ |
‒ |
‒ |
‒ |
‒ |
‒ |
m5 |
m6 |
+12 +4 |
20 15 4 |
+15 +6 |
23 17 6 |
+18 +7 |
26 20 7 |
+21 +8 |
31 23 8 |
+25 +9 |
37 27 9 |
+30 +11 |
45 34 11 |
m6 |
+30 +11 |
45 34 11 |
+35 +13 |
55 42 13 |
+35 +13 |
55 42 13 |
+40 +15 |
65 48 15 |
+40 +15 |
65 48 15 |
m6 |
+40 +15 |
65 48 15 |
+46 +17 |
76 56 17 |
+46 +17 |
76 56 17 |
+46 +17 |
76 56 17 |
+52 +20 |
87 65 20 |
m6 |
+52 +20 |
87 65 20 |
+57 +21 |
97 72 21 |
+57 +21 |
97 72 21 |
+63 +23 |
108 80 23 |
+63 +23 |
108 80 23 |
m6 |
+70 +26 |
120 88 26 |
+70 +26 |
120 88 26 |
+80 +30 |
155 113 30 |
+80 +30 |
155 113 30 |
+90 +34 |
190 138 34 |
m6 |
n5 |
+13 +8 |
21 17 8 |
+16 +10 |
24 19 10 |
+20 +12 |
28 23 12 |
+24 +15 |
34 28 15 |
+28 +17 |
40 32 17 |
+33 +20 |
48 39 20 |
n5 |
+33 +20 |
48 39 20 |
+38 +23 |
58 46 23 |
+38 +23 |
58 46 23 |
+45 +27 |
70 56 27 |
+45 +27 |
70 56 27 |
n5 |
+45 +27 |
70 56 27 |
+51 +31 |
81 64 31 |
+51 +31 |
81 64 31 |
+51 +31 |
81 64 31 |
+57 +34 |
92 73 34 |
n5 |
+57 +34 |
92 73 34 |
+62 +37 |
102 80 37 |
+62 +37 |
102 80 37 |
+67 +40 |
112 88 40 |
+67 +40 |
112 88 40 |
n5 |
‒ |
‒ |
‒ |
‒ |
‒ |
‒ |
‒ |
‒ |
‒ |
‒ |
n5 |
n6 |
+16 +8 |
24 19 8 |
+19 +10 |
27 21 10 |
+23 +12 |
31 25 12 |
+28 +15 |
38 30 15 |
+33 +17 |
45 36 17 |
+39 +20 |
54 43 20 |
n6 |
+39 +20 |
54 43 20 |
+45 +23 |
65 51 23 |
+45 +23 |
65 51 23 |
+52 +27 |
77 60 27 |
+52 +27 |
77 60 27 |
n6 |
+52 +27 |
77 60 27 |
+60 +31 |
90 70 31 |
+60 +31 |
90 70 31 |
+60 +31 |
90 70 31 |
+66 +34 |
101 79 34 |
n6 |
+66 +34 |
101 79 34 |
+73 +37 |
113 88 37 |
+73 +37 |
113 88 37 |
+80 +40 |
125 97 40 |
+80 +40 |
125 97 40 |
n6 |
+88 +44 |
138 106 44 |
+88 +44 |
138 106 44 |
+100 +50 |
175 133 50 |
+100 +50 |
175 133 50 |
+112 +56 |
212 160 56 |
n6 |
p6 |
+20 +12 |
28 23 12 |
+24 +15 |
32 26 15 |
+29 +18 |
37 31 18 |
+35 +22 |
45 37 22 |
+42 +26 |
54 45 26 |
+51 +32 |
66 55 32 |
p6 |
+51 +32 |
66 55 32 |
+59 +37 |
79 65 37 |
+59 +37 |
79 65 37 |
+68 +43 |
93 76 43 |
+68 +43 |
93 76 43 |
p6 |
+68 +43 |
93 76 43 |
+79 +50 |
109 89 50 |
+79 +50 |
109 89 50 |
+79 +50 |
109 89 50 |
+88 +56 |
123 101 56 |
p6 |
+88 +56 |
123 101 56 |
+98 +62 |
138 113 62 |
+98 +62 |
138 113 62 |
+108 +68 |
153 125 68 |
+108 +68 |
153 125 68 |
p6 |
+122 +78 |
172 140 78 |
+122 +78 |
172 140 78 |
+138 +88 |
213 171 88 |
+138 +88 |
213 171 88 |
+156 +100 |
256 204 100 |
p6 |
Nominal shaft diameter in mm |
|||||||||||||||||||||||||||||||||||||||||||||||||||||||||
over incl. |
3 6 |
6 10 |
10 18 |
18 30 |
30 50 |
50 65 |
over incl. |
65 80 |
80 100 |
100 120 |
120 140 |
140 160 |
over incl. |
160 180 |
180 200 |
200 220 |
220 250 |
250 280 |
over incl. |
280 315 |
315 355 |
355 400 |
400 450 |
450 500 |
over incl. |
500 560 |
560 630 |
630 710 |
710 800 |
800 900 |
over incl. |
||||||||||||||||||||||||||
Deviations of bearing bore diameter in μm (tolerance class Normal) |
|||||||||||||||||||||||||||||||||||||||||||||||||||||||||
tΔdmp |
0 –8 |
0 –8 |
0 –8 |
0 –10 |
0 –12 |
0 –15 |
tΔdmp |
0 –15 |
0 –20 |
0 –20 |
0 –25 |
0 –25 |
tΔdmp |
0 –25 |
0 –30 |
0 –30 |
0 –30 |
0 –35 |
tΔdmp |
0 –35 |
0 –40 |
0 –40 |
0 –45 |
0 –45 |
tΔdmp |
0 –50 |
0 –50 |
0 –75 |
0 –75 |
0 –100 |
tΔdmp |
||||||||||||||||||||||||||
Shaft deviation, fit interference or fit clearance in μm |
|||||||||||||||||||||||||||||||||||||||||||||||||||||||||
p7 |
+24 +12 |
32 25 12 |
+30 +15 |
38 30 15 |
+36 +18 |
44 35 18 |
+43 +22 |
53 43 22 |
+51 +26 |
63 51 26 |
+62 +32 |
77 62 32 |
p7 |
+62 +32 |
77 62 32 |
+72 +37 |
92 73 37 |
+72 +37 |
92 73 37 |
+83 +43 |
108 87 43 |
+83 +43 |
108 87 43 |
p7 |
+83 +43 |
108 87 43 |
+96 +50 |
126 101 50 |
+96 +50 |
126 101 50 |
+96 +50 |
126 101 50 |
+108 +56 |
143 114 56 |
p7 |
+108 +56 |
143 114 56 |
+119 +62 |
159 127 62 |
+119 +62 |
159 127 62 |
+131 +68 |
176 139 68 |
+131 +68 |
176 139 68 |
p7 |
+148 +78 |
198 158 78 |
+148 +78 |
198 158 78 |
+168 +88 |
243 199 88 |
+168 +88 |
243 199 88 |
+190 +100 |
290 227 100 |
p7 |
r6 |
+23 +15 |
31 25 15 |
+28 +19 |
36 30 19 |
+34 +23 |
42 35 23 |
+41 +28 |
51 44 28 |
+50 +34 |
62 53 34 |
+60 +41 |
75 64 41 |
r6 |
+62 +43 |
77 66 43 |
+73 +51 |
93 79 51 |
+76 +54 |
96 82 54 |
+88 +63 |
113 97 63 |
+90 +65 |
115 99 65 |
r6 |
+93 +68 |
118 102 68 |
+106 +77 |
136 116 77 |
+109 +80 |
139 119 80 |
+113 +84 |
143 123 84 |
+126 +94 |
161 138 94 |
r6 |
+130 +98 |
165 142 98 |
+144 +108 |
184 159 108 |
+150 +114 |
190 165 114 |
+166 +126 |
211 183 126 |
+172 +132 |
217 189 132 |
r6 |
+194 +150 |
244 212 150 |
+199 +155 |
249 217 155 |
+225 +175 |
300 258 175 |
+235 +185 |
310 268 185 |
+266 +210 |
366 314 210 |
r6 |
r7 |
+27 +15 |
35 28 15 |
+34 +19 |
42 34 19 |
+41 +23 |
49 40 23 |
+49 +28 |
59 49 28 |
+59 +34 |
71 59 34 |
+71 +41 |
86 71 41 |
r7 |
+73 +43 |
88 73 43 |
+86 +51 |
106 87 51 |
+89 +54 |
109 90 54 |
+103 +63 |
128 107 63 |
+105 +65 |
130 109 65 |
r7 |
+108 +68 |
133 112 68 |
+123 +77 |
153 128 77 |
+126 +80 |
156 131 80 |
+130 +84 |
160 135 84 |
+146 +94 |
181 152 94 |
r7 |
+150 +98 |
185 156 98 |
+165 +108 |
205 173 108 |
+171 +114 |
211 179 114 |
+189 +126 |
234 198 126 |
+195 +132 |
240 204 132 |
r7 |
+220 +150 |
270 230 150 |
+225 +155 |
275 235 155 |
+255 +175 |
330 278 175 |
+265 +185 |
340 288 185 |
+300 +210 |
400 337 210 |
r7 |
s6 |
+27 +19 |
35 30 19 |
+32 +23 |
40 34 23 |
+39 +28 |
47 41 28 |
+48 +35 |
58 50 35 |
+59 +43 |
71 62 43 |
+72 +53 |
87 76 53 |
s6 |
+78 +59 |
93 82 59 |
+93 +71 |
113 99 71 |
+101 +79 |
121 107 79 |
+117 +92 |
142 125 92 |
+125 +100 |
150 133 100 |
s6 |
+133 +108 |
158 141 108 |
+151 +122 |
181 161 122 |
+159 +130 |
189 169 130 |
+169 +140 |
199 179 140 |
+190 +158 |
225 203 158 |
s6 |
+202 +170 |
237 215 170 |
+226 +190 |
266 241 190 |
+244 +208 |
284 259 208 |
+272 +232 |
317 289 232 |
+292 +252 |
337 309 252 |
s6 |
+324 +280 |
374 343 280 |
+354 +310 |
404 373 310 |
+390 +340 |
465 423 340 |
+430 +380 |
505 463 380 |
+486 +430 |
586 534 430 |
s6 |
Example
Example: |
||||||
Maximum material value |
+6 |
18 |
Interference or fit clearance if the maximum material values are combined. Probable interference or fit clearance |
|||
Minimum material value |
–5 |
5 |
Interference or fit clearance if the minimum material values are combined |
|||
Values in bold type in the group of three indicate fit interference, values in normal type indicate fit clearance. |
Housing fits
Nominal housing bore diameter in mm |
Nominal housing bore diameter in mm |
||||||||||||||||||||||||||||||||
---|---|---|---|---|---|---|---|---|---|---|---|---|---|---|---|---|---|---|---|---|---|---|---|---|---|---|---|---|---|---|---|---|---|
over incl. |
6 10 |
10 18 |
18 30 |
30 50 |
50 80 |
80 120 |
120 150 |
150 180 |
over incl. |
180 250 |
250 315 |
315 400 |
400 500 |
500 630 |
630 800 |
800 1 000 |
1 000 1 250 |
||||||||||||||||
Deviations of bearing outside diameter in μm (tolerance class Normal) |
Deviations of bearing outside diameter in μm (tolerance class Normal) |
||||||||||||||||||||||||||||||||
tΔDmp |
0 –8 |
0 –8 |
0 –9 |
0 –11 |
0 –13 |
0 –15 |
0 –18 |
0 –25 |
tΔDmp |
0 –30 |
0 –35 |
0 –40 |
0 –45 |
0 –50 |
0 –75 |
0 –100 |
0 –125 |
||||||||||||||||
Housing deviation, fit interference or fit clearance in μm |
Housing deviation, fit interference or fit clearance in μm |
||||||||||||||||||||||||||||||||
E8 |
+47 +25 |
25 35 55 |
+59 +32 |
32 44 67 |
+73 +40 |
40 54 82 |
+89 +50 |
50 67 100 |
+106 +60 |
60 79 119 |
+126 +72 |
72 85 141 |
+148 +85 |
85 112 166 |
+148 +85 |
85 114 173 |
E8 |
+172 +100 |
100 134 202 |
+191 +110 |
110 149 226 |
+214 +125 |
125 168 254 |
+232 +135 |
135 182 277 |
+255 +145 |
145 199 305 |
+285 +160 |
160 227 360 |
+310 +170 |
170 250 410 |
+360 +195 |
195 292 485 |
F7 |
+28 +13 |
13 21 36 |
+34 +16 |
16 25 42 |
+41 +20 |
20 30 50 |
+50 +25 |
25 37 61 |
+60 +30 |
30 44 73 |
+71 +36 |
36 53 86 |
+83 +43 |
43 62 101 |
+83 +43 |
43 64 108 |
F7 |
+96 +50 |
50 75 126 |
+108 +56 |
56 85 143 |
+119 +62 |
62 94 159 |
+131 +68 |
68 104 176 |
+146 +76 |
76 116 196 |
+160 +80 |
80 132 235 |
+176 +86 |
86 149 276 |
+203 +98 |
98 175 328 |
G6 |
+14 +5 |
5 11 22 |
+17 +6 |
6 12 25 |
+20 +7 |
7 14 29 |
+25 +9 |
9 18 36 |
+29 +10 |
10 21 42 |
+34 +12 |
12 24 49 |
+39 +14 |
14 28 57 |
+39 +14 |
14 31 64 |
G6 |
+44 +15 |
15 35 74 |
+49 +17 |
17 39 84 |
+54 +18 |
18 43 94 |
+60 +20 |
20 48 105 |
+66 +22 |
22 54 116 |
+74 +24 |
24 66 149 |
+82 +26 |
26 78 182 |
+94 +28 |
28 93 219 |
G7 |
+20 +5 |
5 13 28 |
+24 +6 |
6 15 32 |
+28 +7 |
7 17 37 |
+34 +9 |
9 21 45 |
+40 +10 |
10 24 53 |
+47 +12 |
12 29 62 |
+54 +14 |
14 33 72 |
+54 +14 |
14 36 79 |
G7 |
+61 +15 |
15 40 91 |
+69 +17 |
17 46 104 |
+75 +18 |
18 50 115 |
+83 +20 |
20 56 128 |
+92 +22 |
22 62 142 |
+104 +24 |
24 76 179 |
+116 +26 |
26 89 216 |
+133 +28 |
28 105 258 |
H6 |
+9 0 |
0 6 17 |
+11 0 |
0 6 19 |
+13 0 |
0 7 22 |
+16 0 |
0 9 27 |
+19 0 |
0 11 32 |
+22 0 |
0 12 37 |
+25 0 |
0 14 43 |
+25 0 |
0 17 50 |
H6 |
+29 0 |
0 20 59 |
+32 0 |
0 22 67 |
+36 0 |
0 25 76 |
+40 0 |
0 28 85 |
+44 0 |
0 32 94 |
+50 0 |
0 42 125 |
+56 0 |
0 52 156 |
+66 0 |
0 64 191 |
Nominal housing bore diameter in mm |
|||||||||||||||||||||||||||||||||
over incl. |
6 10 |
10 18 |
18 30 |
30 50 |
50 80 |
80 120 |
120 150 |
150 180 |
over incl. |
180 250 |
250 315 |
315 400 |
400 500 |
500 630 |
630 800 |
800 1 000 |
1 000 1 250 |
||||||||||||||||
Deviations of bearing outside diameter in μm (tolerance class Normal) |
|||||||||||||||||||||||||||||||||
tΔDmp |
0 –8 |
0 –8 |
0 –9 |
0 –11 |
0 –13 |
0 –15 |
0 –18 |
0 –25 |
tΔDmp |
0 –30 |
0 –35 |
0 –40 |
0 –45 |
0 –50 |
0 –75 |
0 –100 |
0 –125 |
||||||||||||||||
Housing deviation, fit interference or fit clearance in μm |
|||||||||||||||||||||||||||||||||
H7 |
+15 0 |
0 8 23 |
+18 0 |
0 9 26 |
+21 0 |
0 10 30 |
+25 0 |
0 12 36 |
+30 0 |
0 14 43 |
+35 0 |
0 17 50 |
+40 0 |
0 19 58 |
+40 0 |
0 22 65 |
H7 |
+46 0 |
0 25 76 |
+52 0 |
0 29 87 |
+57 0 |
0 32 97 |
+63 0 |
0 36 108 |
+70 0 |
0 40 120 |
+80 0 |
0 52 155 |
+90 0 |
0 63 190 |
+105 0 |
0 77 230 |
H8 |
+22 0 |
0 10 30 |
+27 0 |
0 12 35 |
+33 0 |
0 14 42 |
+39 0 |
0 17 50 |
+46 0 |
0 20 59 |
+54 0 |
0 23 69 |
+63 0 |
0 27 81 |
+63 0 |
0 29 88 |
H8 |
+72 0 |
0 34 102 |
+81 0 |
0 39 116 |
+89 0 |
0 43 129 |
+97 0 |
0 47 142 |
+110 0 |
0 54 160 |
+125 0 |
0 67 200 |
+140 0 |
0 80 240 |
+165 0 |
0 97 290 |
J6 |
+5 –4 |
4 2 13 |
+6 –5 |
5 1 14 |
+8 –5 |
5 2 17 |
+10 –6 |
6 3 21 |
+13 –6 |
6 5 26 |
+16 –6 |
6 6 31 |
+18 –7 |
7 7 36 |
+18 –7 |
7 10 43 |
J6 |
+22 –7 |
7 13 52 |
+25 –7 |
7 15 60 |
+29 –7 |
7 18 69 |
+33 –7 |
7 21 78 |
‒ |
‒ |
‒ |
‒ |
‒ |
‒ |
‒ |
‒ |
J7 |
+8 –7 |
7 1 16 |
+10 –8 |
8 1 18 |
+12 –9 |
9 1 21 |
+14 –11 |
11 1 25 |
+18 –12 |
12 2 31 |
+22 –13 |
13 4 37 |
+26 –14 |
14 5 44 |
+26 –14 |
14 8 51 |
J7 |
+30 –16 |
16 9 60 |
+36 –16 |
16 13 71 |
+39 –18 |
18 14 79 |
+43
–20 |
20 16 88 |
‒ |
‒ |
‒ |
‒ |
‒ |
‒ |
‒ |
‒ |
JS6 |
+4,5 –4,5 |
4,5 2 12,5 |
+5,5 –5,5 |
5,5 1 13,5 |
+6,5 –6,5 |
6,5 0 15,5 |
+8 –8 |
8 1 19 |
+9,5 –9,5 |
9,5 0 22,5 |
+11 –11 |
11 1 26 |
+12,5 –12,5 |
12,5 1 30,5 |
+12,5 –12,5 |
12,5 3 37,5 |
JS6 |
+14,5 –14,5 |
14,5 5 44,5 |
+16 –16 |
16 7 51 |
+18 –18 |
18 6 58 |
+20 –20 |
20 8 65 |
+22 –22 |
22 10 72 |
+25 –25 |
25 17 100 |
+28 –28 |
28 24 128 |
+33 –33 |
33 31 158 |
Nominal housing bore diameter in mm |
|||||||||||||||||||||||||||||||||
over incl. |
6 10 |
10 18 |
18 30 |
30 50 |
50 80 |
80 120 |
120 150 |
150 180 |
over incl. |
180 250 |
250 315 |
315 400 |
400 500 |
500 630 |
630 800 |
800 1 000 |
1 000 1 250 |
||||||||||||||||
Deviations of bearing outside diameter in μm (tolerance class Normal) |
|||||||||||||||||||||||||||||||||
tΔDmp |
0 –8 |
0 –8 |
0 –9 |
0 –11 |
0 –13 |
0 –15 |
0 –18 |
0 –25 |
tΔDmp |
0 –30 |
0 –35 |
0 –40 |
0 –45 |
0 –50 |
0 –75 |
0 –100 |
0 –125 |
||||||||||||||||
Housing deviation, fit interference or fit clearance in μm |
|||||||||||||||||||||||||||||||||
JS7 |
+7,5 –7,5 |
7,5 1 15,5 |
+9 –9 |
9 0 17 |
+10,5 –10,5 |
10,5 1 19,5 |
+12,5 –12,5 |
12,5 1 23,5 |
+15 –15 |
15 1 28 |
+17,5 –17,5 |
17,5 1 32,5 |
+20 –20 |
20 1 38 |
+20 –20 |
20 1 45 |
JS7 |
+23 –23 |
23 2 53 |
+26 –26 |
26 3 61 |
+28,5 –28,5 |
28,5 3 68,5 |
+31,5 –31,5 |
31,5 4 76,5 |
+35 –35 |
35 5 85 |
+40 –40 |
40 12 115 |
+45 –45 |
45 18 145 |
+52,5 –52,5 |
52 24 177 |
K6 |
+2 –7 |
7 1 10 |
+2 –9 |
9 3 10 |
+2 –11 |
11 4 11 |
+3 –13 |
13 4 14 |
+4 –15 |
15 4 17 |
+4 –18 |
18 6 19 |
+4 –21 |
21 7 22 |
+4 –21 |
21 4 29 |
K6 |
+5 –24 |
24 4 35 |
+5 –27 |
27 5 40 |
+7 –29 |
29 4 47 |
+8 –32 |
32 4 53 |
0 –44 |
44 12 50 |
0 –50 |
50 8 75 |
0 –56 |
56 4 100 |
0 –66 |
66 2 125 |
K7 |
+5 –10 |
10 2 13 |
+6 –12 |
12 3 14 |
+6 –15 |
15 5 15 |
+7 –18 |
18 6 18 |
+9 –21 |
21 7 22 |
+10 –25 |
25 8 25 |
+12 –28 |
28 9 30 |
+12 –28 |
28 6 37 |
K7 |
+13 –33 |
33 8 43 |
+16 –36 |
36 7 51 |
+17 –40 |
40 8 57 |
+18 –45 |
45 9 63 |
0 –70 |
70 30 50 |
0 –80 |
80 28 75 |
0 –90 |
90 27 100 |
0 –105 |
105 28 125 |
M6 |
–3 –12 |
12 6 5 |
–4 –15 |
15 9 4 |
–4 –17 |
17 10 5 |
–4 –20 |
20 11 7 |
–5 –24 |
24 13 8 |
–6 –28 |
28 16 9 |
–8 –33 |
33 19 10 |
–8 –33 |
33 16 17 |
M6 |
–8 –37 |
37 17 22 |
–9 –41 |
41 19 26 |
–10 –46 |
46 21 30 |
–10 –50 |
50 22 35 |
–26 –70 |
70 38 24 |
–30 –80 |
80 38 45 |
–34 –90 |
90 38 66 |
–40 –106 |
106 45 85 |
M7 |
0 –15 |
15 7 8 |
0 –18 |
18 9 8 |
0 –21 |
21 11 9 |
0 –25 |
25 13 11 |
0 –30 |
30 16 13 |
0 –35 |
35 18 15 |
0 –40 |
40 21 18 |
0 –40 |
40 18 25 |
M7 |
0 –46 |
46 21 30 |
0 –52 |
52 23 35 |
0 –57 |
57 25 40 |
0 –63 |
63 27 45 |
–26 –96 |
96 56 24 |
–30 –110 |
110 58 45 |
–34 –124 |
124 61 66 |
–40 –145 |
145 68 85 |
Nominal housing bore diameter in mm |
|||||||||||||||||||||||||||||||||
over incl. |
6 10 |
10 18 |
18 30 |
30 50 |
50 80 |
80 120 |
120 150 |
150 180 |
over incl. |
180 250 |
250 315 |
315 400 |
400 500 |
500 630 |
630 800 |
800 1 000 |
1 000 1 250 |
||||||||||||||||
Deviations of bearing outside diameter in μm (tolerance class Normal) |
|||||||||||||||||||||||||||||||||
tΔDmp |
0 –8 |
0 –8 |
0 –9 |
0 –11 |
0 –13 |
0 –15 |
0 –18 |
0 –25 |
tΔDmp |
0 –30 |
0 –35 |
0 –40 |
0 –45 |
0 –50 |
0 –75 |
0 –100 |
0 –125 |
||||||||||||||||
Housing deviation, fit interference or fit clearance in μm |
|||||||||||||||||||||||||||||||||
N6 |
–7 –16 |
16 10 1 |
–9 –20 |
20 14 1 |
–11 –24 |
24 17 2 |
–12 –28 |
28 19 1 |
–14 –33 |
33 22 1 |
–16 –38 |
38 26 1 |
–20 –45 |
45 31 2 |
–20 –45 |
45 28 5 |
N6 |
–22 –51 |
51 31 8 |
–25 –57 |
57 35 10 |
–26 –62 |
62 37 14 |
–27 –67 |
67 39 18 |
–44 –88 |
88 56 6 |
–50 –100 |
100 58 25 |
–56 –112 |
112 60 44 |
–66 –132 |
132 67 59 |
N7 |
–4 –19 |
19 11 4 |
–5 –23 |
23 14 3 |
–7 –28 |
28 18 2 |
–8 –33 |
33 21 3 |
–9 –39 |
39 25 4 |
–10 –45 |
45 28 5 |
–12 –52 |
52 33 3 |
–12 –52 |
52 30 13 |
N7 |
–14 –60 |
60 35 16 |
–14 –66 |
66 37 21 |
–16 –73 |
73 41 24 |
–17 –80 |
80 44 28 |
–44 –114 |
114 74 6 |
–50 –130 |
130 78 25 |
–56 –146 |
146 83 44 |
–66 –171 |
171 94 59 |
P6 |
–12 –21 |
21 15 4 |
–15 –26 |
26 20 7 |
–18 –31 |
31 24 9 |
–21 –37 |
37 28 10 |
–26 –45 |
45 34 13 |
–30 –52 |
52 40 15 |
–36 –61 |
61 47 18 |
–36 –61 |
61 44 11 |
P6 |
–41 –70 |
70 50 11 |
–47 –79 |
79 57 12 |
–51 –87 |
87 62 11 |
–55 –95 |
95 67 10 |
–78 –122 |
122 90 28 |
–88 –138 |
138 96 13 |
–100 –156 |
156 104 0 |
–120 –186 |
186 121 5 |
P7 |
–9 –24 |
24 16 1 |
–11 –29 |
29 20 3 |
–14 –35 |
35 25 5 |
–17 –42 |
42 30 6 |
–21 –51 |
51 37 8 |
–24 –59 |
59 42 9 |
–28 –68 |
68 49 10 |
–28 –68 |
68 46 3 |
P7 |
–33 –79 |
79 54 3 |
–36 –88 |
88 59 1 |
–41 –98 |
98 66 1 |
–45 –108 |
108 72 0 |
–78 –148 |
148 108 28 |
–88 –168 |
168 126 13 |
–100 –190 |
190 127 0 |
–120 –225 |
225 148 5 |
Example
Housing ⌀ 100 K6 Ⓔ |
||||||
Minimum material value |
+4 |
18 |
Interference or fit clearance if the maximum material values are combined. Probable interference or fit clearance |
|||
Maximum material value |
–18 |
19 |
Interference or fit clearance if the minimum material values are combined |
|||
Values in bold type in the group of three indicate fit interference, values in normal type indicate fit clearance. |
Shaft tolerances for adapter sleeves and withdrawal sleeves are shown in ➤ Table.
Shaft tolerances for adapter sleeves and withdrawal sleeves
Nominal |
Shaft tolerance |
||||||
---|---|---|---|---|---|---|---|
h7/ |
h8/ |
h9/ |
|||||
mm |
μm |
μm |
μm |
||||
over |
incl. |
||||||
3 |
6 |
0 –12 |
2,5 |
0 –18 |
2,5 |
0 –30 |
4 |
6 |
10 |
0 –15 |
3 |
0 –22 |
3 |
0 –36 |
4,5 |
10 |
18 |
0 –18 |
4 |
0 –27 |
4 |
0 –43 |
5,5 |
18 |
30 |
0 –21 |
4,5 |
0 –33 |
4,5 |
0 –52 |
6,5 |
30 |
50 |
0 –25 |
5,5 |
0 –39 |
5,5 |
0 –62 |
8 |
50 |
65 |
0 –30 |
6,5 |
0 –46 |
6,5 |
0 –74 |
9,5 |
65 |
80 |
0 –30 |
6,5 |
0 –46 |
6,5 |
0 –74 |
9,5 |
80 |
100 |
0 –35 |
7,5 |
0 –54 |
7,5 |
0 –87 |
11 |
100 |
120 |
0 –35 |
7,5 |
0 –54 |
7,5 |
0 –87 |
11 |
120 |
140 |
0 –40 |
9 |
0 –63 |
9 |
0 –100 |
12,5 |
140 |
160 |
0 –40 |
9 |
0 –63 |
9 |
0 –100 |
12,5 |
160 |
180 |
0 –40 |
9 |
0 –63 |
9 |
0 –100 |
12,5 |
180 |
200 |
0 –46 |
10 |
0 –72 |
10 |
0 –115 |
14,5 |
200 |
220 |
0 –46 |
10 |
0 –72 |
10 |
0 –115 |
14,5 |
220 |
250 |
0 –46 |
10 |
0 –72 |
10 |
0 –115 |
14,5 |
250 |
280 |
0 –52 |
11,5 |
0 –81 |
11,5 |
0 –130 |
16 |
280 |
315 |
0 –52 |
11,5 |
0 –81 |
11,5 |
0 –130 |
16 |
315 |
355 |
0 –57 |
12,5 |
0 –89 |
12,5 |
0 –140 |
18 |
355 |
400 |
0 –57 |
12,5 |
0 –89 |
12,5 |
0 –140 |
18 |
400 |
450 |
0 –63 |
13,5 |
0 –97 |
13,5 |
0 –155 |
20 |
450 |
500 |
0 –63 |
13,5 |
0 –97 |
13,5 |
0 –155 |
20 |
500 |
560 |
0 –70 |
16 |
0 –110 |
16 |
0 –175 |
22 |
560 |
630 |
0 –70 |
16 |
0 –110 |
16 |
0 –175 |
22 |
630 |
710 |
0 –80 |
18 |
0 –125 |
18 |
0 –200 |
25 |
710 |
800 |
0 –80 |
18 |
0 –125 |
18 |
0 –200 |
25 |
800 |
900 |
0 –90 |
20 |
0 –140 |
20 |
0 –230 |
28 |
The numbers printed in italics give guide values for the cylindricity tolerance t1 (DIN EN ISO 1101) ➤ Figure.
Enveloping circle
For bearings without an inner ring, the enveloping circle Fw ➤ Figure is used. This is the inner inscribed circle of the rolling elements in clearance-free contact with the outer raceway. The enveloping circle for unfitted machined needle roller bearings is in the tolerance class F6 and for drawn cup needle roller bearings in the tolerance class F8. Deviations for F6 and F8 ➤ Table.
Enveloping circle Fw = enveloping circle diameter
|
![]() |
Deviations for the enveloping circle diameter
Enveloping |
Tolerance class F6 |
Tolerance class F8 |
|||
---|---|---|---|---|---|
mm |
Tolerance for enveloping circle diameter Fw |
Tolerance for enveloping circle diameter Fw |
|||
Upper deviation |
Lower deviation |
Upper deviation |
Lower deviation |
||
over |
incl. |
μm |
μm |
μm |
μm |
3 |
6 |
+18 |
+10 |
+28 |
+10 |
6 |
10 |
+22 |
+13 |
+35 |
+13 |
10 |
18 |
+27 |
+16 |
+43 |
+16 |
18 |
30 |
+33 |
+20 |
+53 |
+20 |
30 |
50 |
+41 |
+25 |
+64 |
+25 |
50 |
80 |
+49 |
+30 |
+76 |
+30 |
80 |
120 |
+58 |
+36 |
+90 |
+36 |
120 |
180 |
+68 |
+43 |
+106 |
+43 |
180 |
250 |
+79 |
+50 |
+122 |
+50 |
250 |
315 |
+88 |
+56 |
+137 |
+56 |
315 |
400 |
+98 |
+62 |
+151 |
+62 |
400 |
500 |
+108 |
+68 |
+165 |
+68 |
Dimensional, geometrical and running accuracy of mating parts
In order to achieve the required fit, the bearing seats and fit surfaces of the shaft and housing bore must conform to certain tolerances ➤ Figure and ➤ Table.
Guide values for the geometrical and positional tolerances of bearing seating surfaces t1 = roundness tolerance t2 = parallelism tolerance t3 = total axial runout tolerance of abutment shoulders t4 = coaxiality tolerance |
![]() |
Accuracy of bearing seating surfaces
ISO fundamental tolerances
The degree of accuracy for the bearing seat tolerances on the shaft and in the housing, as well as the ISO fundamental tolerances, are shown in ➤ Table (DIN ISO 286-1:2010).
Second bearing seat
The positional tolerances t4 for a second bearing seat on the shaft (d2) or in the housing (D2) are dependent on the types of bearings used and the operating conditions.
Housings
In split housings, the joints must be free from burrs. The accuracy of the bearing seats is determined as a function of the accuracy of the bearing selected.
Guide values for the geometrical and positional tolerances of bearing seating surfaces
Bearing |
Bearing seating surface |
Fundamental tolerance grades1) |
||||
---|---|---|---|---|---|---|
to ISO 492 |
to DIN 620 |
Diameter tolerance |
Roundness tolerance |
Parallelism tolerance |
Total |
|
t1 |
t2 |
t3 |
||||
Normal 6X |
PN (P0) P6X |
Shaft |
IT6 (IT5) |
Circumferential load IT4/2 |
Circumferential load IT4/2 |
IT4 |
Shaft | IT6 (IT5) |
Point load IT5/2 |
Point load IT5/2 |
IT4 | ||
Housing |
IT7 (IT6) |
Circumferential load IT5/2 |
Circumferential load IT5/2 |
IT5 | ||
Housing | IT7 (IT6) |
Point load IT6/2 |
Point load IT6/2 |
IT5 | ||
6 |
P6 |
Shaft |
IT5 |
Circumferential load IT3/2 |
Circumferential load IT3/2 |
IT3 |
Shaft | IT5 |
Point load IT4/2 |
Point load IT4/2 |
IT3 | ||
Housing |
IT6 |
Circumferential load IT4/2 |
Circumferential load IT4/2 |
IT4 | ||
Housing | IT6 |
Point load IT5/2 |
Point load IT5/2 |
IT4 | ||
5 |
P5 |
Shaft |
IT5 |
Circumferential load IT2/2 |
Circumferential load IT2/2 |
IT2 |
Shaft | IT5 |
Point load IT3/2 |
Point load IT3/2 |
IT2 | ||
Housing |
IT6 |
Circumferential load IT3/2 |
Circumferential load IT3/2 |
IT3 | ||
Housing | IT6 |
Point load IT4/2 |
Point load IT4/2 |
IT3 | ||
4 |
P4 P4S2) SP2) |
Shaft |
IT4 |
Circumferential load IT1/2 |
Circumferential load IT1/2 |
IT1 |
Shaft | IT4 |
Point load IT2/2 |
Point load IT2/2 |
IT1 | ||
Housing |
IT5 |
Circumferential load IT2/2 |
Circumferential load IT2/2 |
IT2 | ||
Housing | IT5 |
Point load IT3/2 |
Point load IT3/2 |
IT2 | ||
UP2) |
Shaft |
IT3 |
Circumferential load IT0/2 |
Circumferential load IT0/2 |
IT0 | |
Shaft | IT3 |
Point load IT1/2 |
Point load IT1/2 |
IT0 | ||
Housing |
IT4 |
Circumferential load IT1/2 |
Circumferential load IT1/2 |
IT1 | ||
Housing | IT4 |
Point load IT2/2 |
Point load IT2/2 |
IT1 |
- ISO fundamental tolerances (IT grades) in accordance with DIN ISO 286. Values for IT grades ➤ Table.
- Not included in DIN 620.
Roughness of bearing seats
Ra must not be too high
The roughness of the bearing seats must be matched to the tolerance class of the bearings. The mean roughness value Ra must not be too high, in order to maintain the interference loss within limits. Shafts must be ground, while bores must be precision turned. For further information on this subject ➤ Table and product chapter.
Roughness values for cylindrical bearing seating surfaces – guide values
Nominal diameter d (D) |
Recommended mean roughness value Ramax |
||||
---|---|---|---|---|---|
mm |
μm |
||||
Diameter tolerance (IT grade) |
|||||
over |
incl. |
IT7 |
IT6 |
IT5 |
IT4 |
‒ |
80 |
1,6 |
0,8 |
0,4 |
0,2 |
80 |
500 |
1,6 |
1,6 |
0,8 |
0,4 |
500 |
1 250 |
3,21) |
1,6 |
1,6 |
0,8 |
- For the mounting of bearings using the hydraulic method, a value Ra = 1,6 μm must not be exceeded
Numerical values for IT grades
➤ Table shows numerical values for the ISO fundamental tolerances (IT grades) in accordance with DIN ISO 286-1:2010.
IT grades and values
IT grade |
Nominal dimension in mm |
||||||||
---|---|---|---|---|---|---|---|---|---|
over |
– |
3 |
6 |
10 |
18 |
30 |
50 |
80 |
|
incl. |
3 |
6 |
10 |
18 |
30 |
50 |
80 |
120 |
|
Values in μm |
|||||||||
IT01 |
0,3 |
0,4 |
0,4 |
0,5 |
0,6 |
0,6 |
0,8 |
1 |
|
IT0 |
0,5 |
0,6 |
0,6 |
0,8 |
1 |
1 |
1,2 |
1,5 |
|
IT1 |
0,8 |
1 |
1 |
1,2 |
1,5 |
1,5 |
2 |
2,5 |
|
IT2 |
1,2 |
1,5 |
1,5 |
2 |
2,5 |
2,5 |
3 |
4 |
|
IT3 |
2 |
2,5 |
2,5 |
3 |
4 |
4 |
5 |
6 |
|
IT4 |
3 |
4 |
4 |
5 |
6 |
7 |
8 |
10 |
|
IT5 |
4 |
5 |
6 |
8 |
9 |
11 |
13 |
15 |
|
IT6 |
6 |
8 |
9 |
11 |
13 |
16 |
19 |
22 |
|
IT7 |
10 |
12 |
15 |
18 |
21 |
25 |
30 |
35 |
|
IT8 |
14 |
18 |
22 |
27 |
33 |
39 |
46 |
54 |
|
IT9 |
25 |
30 |
36 |
43 |
52 |
62 |
74 |
87 |
|
IT10 |
40 |
48 |
58 |
70 |
84 |
100 |
120 |
140 |
|
IT11 |
60 |
75 |
90 |
110 |
130 |
160 |
190 |
220 |
|
IT12 |
100 |
120 |
150 |
180 |
210 |
250 |
300 |
350 |
|
continued ▼ |
IT grades and values
IT grade |
Nominal dimension in mm |
||||||||
---|---|---|---|---|---|---|---|---|---|
over |
120 |
180 |
250 |
315 |
400 |
500 |
630 |
800 |
|
incl. |
180 |
250 |
315 |
400 |
500 |
630 |
800 |
1 000 |
|
Values in μm |
|||||||||
IT01 |
1,2 |
2 |
2,5 |
3 |
4 |
‒ |
‒ |
‒ |
|
IT0 |
2 |
3 |
4 |
5 |
6 |
‒ |
‒ |
‒ |
|
IT1 |
3,5 |
4,5 |
6 |
7 |
8 |
9 |
10 |
11 |
|
IT2 |
5 |
7 |
8 |
9 |
10 |
11 |
13 |
15 |
|
IT3 |
8 |
10 |
12 |
13 |
15 |
16 |
18 |
21 |
|
IT4 |
12 |
14 |
16 |
18 |
20 |
22 |
25 |
28 |
|
IT5 |
18 |
20 |
23 |
25 |
27 |
32 |
36 |
40 |
|
IT6 |
25 |
29 |
32 |
36 |
40 |
44 |
50 |
56 |
|
IT7 |
40 |
46 |
52 |
57 |
63 |
70 |
80 |
90 |
|
IT8 |
63 |
72 |
81 |
89 |
97 |
110 |
125 |
140 |
|
IT9 |
100 |
115 |
130 |
140 |
155 |
175 |
200 |
230 |
|
IT10 |
160 |
185 |
210 |
230 |
250 |
280 |
320 |
360 |
|
IT11 |
250 |
290 |
320 |
360 |
400 |
440 |
500 |
560 |
|
IT12 |
400 |
460 |
520 |
570 |
630 |
700 |
800 |
900 |
|
continued ▲ |
Seats for adapter sleeves and withdrawal sleeves
Seat diameter tolerances for adapter sleeves and withdrawal sleeves
Adapter and withdrawal sleeves are used if increased requirements are not made on the running accuracy of the bearing. For the seats, diameter tolerances corresponding to the IT grades 7 to 9 are possible, while the geometrical deviation can be 50% of this value.
Tapered bearing seats for radial bearings
Geometrical and positional tolerances of the shaft
Guide values for the machining of tapered bearing seats on shafts are shown in ➤ Figure, ➤ Table.
This information does not apply to super precision cylindrical roller bearings in machine tools (spindle bearing arrangement). For information on this subject, see the catalogue Super precision bearings SP 1.
Taper gauges
Schaeffler taper gauges can be used to check for adherence to the recommended tolerances.
Guide values for the geometrical and positional tolerances of tapered bearing seats B = bearing width SL = L · taper ratio (1:12, 1:30) tΔSL′ = taper angle tolerance t1 = roundness tolerance t6 = perpendicularity tolerance = 2/3 · t2; z = recommended mean roughness |
![]() |
The tolerances for taper angle tΔSL relative to the bearing width B can be found in the table ➤ Table.
Taper angle tolerance of tapered bearing seats, relative to bearing width
Bearing width B mm |
Taper angle tolerance tΔSL |
||||
from | to | ||||
Deviations | |||||
over | incl. | upper μm |
lower μm |
uper μm |
lower μm |
16 | 25 | +8 | 0 | +12,5 | 0 |
25 | 40 | +10 | 0 | +16 | 0 |
40 | 63 | +12,5 | 0 | +20 | 0 |
63 | 100 | +16 | 0 | +25 | 0 |
100 | 160 | +20 | 0 | +32 | 0 |
160 | 250 | +25 | 0 | +40 | 0 |
250 | 400 | +32 | 0 | +50 | 0 |
400 | 630 | +40 | 0 | +63 | 0 |
Determine tΔSL by means of interpolation
For bearing widths with nominal dimensions between the values listed in the table, the taper angle tolerance tΔSL should be determined by means of interpolation of the upper deviations ➤ Equation.
Interpolation of the taper angle tolerance
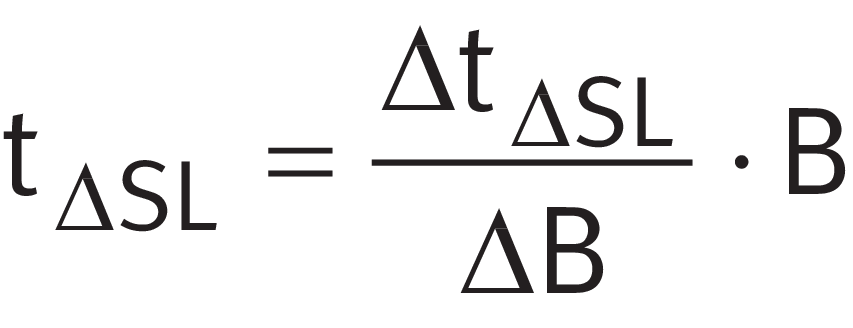
For a taper of length L, the taper angle tolerance tΔSL′ of the entire taper applies ➤ Equation.
Taper angle tolerance of the entire taper

Example of tolerance calculation
Given:
- bearing width B = 90 mm
- taper ratio 1:12
- taper length L = 100 mm

The tolerance tΔSL′/2 is thus 0 to +12 μm.
In order to calculate the taper slope SL (nominal dimension), the taper length L is multiplied by the taper ratio (1:12) ➤ Equation.
Taper slope
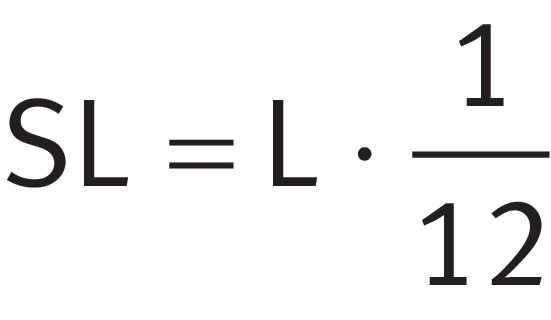
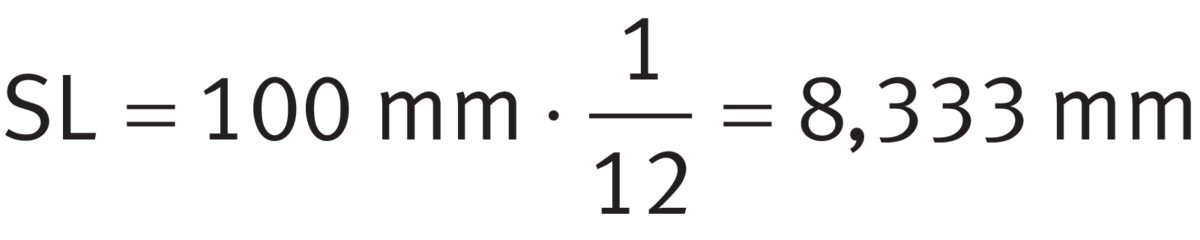
The nominal dimension for SL/2 is thus 4,166 mm; SL/2 = 4,166 +0,012/0.
The data can then be entered in the drawing as follows ➤ Figure.
Example of drawing entry for dimensional tolerances |
![]() |
Checking of a shaft
Measured values:
- d1′ = 120 mm
- d2′ = 128,345 mm
The taper slope is calculated from the measured values using ➤ Equation.
Taper slope
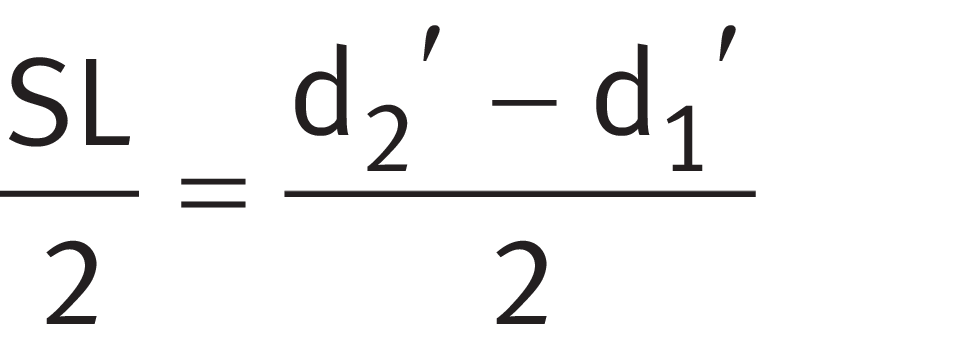

The value for SL/2 is thus within tolerance.
Axial location of bearings
Securing the bearing rings against axial creep by means of form fit
In order to prevent the bearing rings co-rotating, they are radially fixed by means of a tight fit. At the same time, the rings must be axially located in both directions so that they cannot undergo lateral creep. Axial creep cannot be prevented solely by a tight fit, especially not if a radial bearing must support large axial forces. For axial location, the bearing rings must therefore be connected by form fit to the shaft or the housing.
Examples
Solutions proven in practice for individual bearing arrangements (locating bearing arrangement, non-locating bearing arrangement, adjusted/ floating bearing arrangement) and the axial location of bearing rings in certain bearing types are described below. Specific features of the individual bearing types are covered in the product chapters.
Guidelines for axial location of bearing rings
Locating bearing arrangement
Locating bearings can support axial forces in both directions
Locating bearings must in general also support axial forces. For the axial location of bearing rings, form fit elements such as shoulders, snap rings, covers, caps, nuts etc. have proved effective.
➤ Figure shows bearing types that can be used as locating bearings and can support axial forces in both directions. The arrows in ➤ Figure to ➤ Figure indicate what task the axial location methods perform in the various types of mounting and types of bearing, such as axial location on both sides of the outer and inner ring of the deep groove ball bearing.
In locating bearing arrangements, both bearing rings must always be abutted on both sides. The fasteners must be matched to the magnitude of the axial forces present.
Axial location of bearing rings in locating bearings
|
![]() |
Cylindrical roller bearing, deep groove ball bearing
The cylindrical roller bearing NUP and deep groove ball bearing support alternating axial forces. Both rings must therefore be axially located on both sides.
Spherical roller bearing
The spherical roller bearing must, as a locating bearing, support axial forces from alternating directions. In this example, the inner ring is located by means of a withdrawal sleeve.
Angular contact ball bearings
The pair of angular contact ball bearings forms a locating bearing in which the two single row bearings are adjusted against each other in mounting. For location on the shaft, readjustable fasteners, such as nuts, are suitable.
Double direction axial deep groove ball bearing
The double direction axial deep groove ball bearing should be seen as a closed bearing group. The shaft locating washer is axially located on both sides, while the housing locating washers are each located on one side. In order that the ball and cage assemblies are guided correctly in the raceway grooves, the bearing is mounted clearance-free by adjustment of the housing locating washers.
Non-locating bearing arrangement
The means of axial location only needs to prevent lateral creep of the bearing rings
Non-locating bearings must only support slight axial forces. The axial location method only needs to prevent lateral creep of the rings. The simplest way of achieving this is by a tight fit. In the case of non-separable bearings, the rotating bearing ring has a tight fit. The other ring is axially retained by the rolling elements. ➤ Figure shows rolling bearings that can be used as non-locating bearings.
Axial location of bearing rings in non-locating bearings
|
![]() |
Cylindrical roller bearing NU
The cylindrical roller bearing NU is designed such that the inner ring can be displaced relative to the roller and cage assembly. For this reason, both bearing rings must also be secured against axial creep on both sides.
Deep groove ball bearing
In the deep groove ball bearing, only the inner ring is located, while the outer ring is axially retained by the rolling elements.
Spherical roller bearing, barrel roller bearing, angular contact ball bearings
In the spherical roller bearing and barrel roller bearing, as well as in the angular contact ball bearing pair, the outer ring is guided axially by the rolling elements. The inner ring of the barrel roller bearing is located on the shaft with or without an adapter sleeve. Location by means of an adapter sleeve secures the bearing against lateral creep.
Adjusted single row angular contact ball bearings
In the adjusted pair of single row angular contact ball bearings, the inner rings are clamped against each other so that they are not forced apart by the axial component of the radial force.
Adjusted or floating bearing arrangement
The bearings can support axial loads in one direction only
Bearings mounted in an adjusted and floating arrangement can support axial load in one direction only; this also applies to single direction axial bearings. The axial forces are supported by shaft or housing shoulders, snap rings, covers etc.
Angular contact ball bearing, cylindrical roller bearing
The angular contact ball bearing in ➤ Figure supports axial forces in one direction only. The bearing rings therefore only require abutment on one side each in accordance with the force pattern. The axial force component is supported by an additional bearing in a mirror image arrangement. Similar conditions are present in the cylindrical roller bearing NJ.
Axial deep groove ball bearing
The balls in the axial deep groove ball bearing in ➤ Figure only roll correctly if the bearing runs clearance-free and with adequate minimum load.
If the shaft is horizontal, a further adjustable bearing must be provided. This is particularly important in the case of high speeds. If the shaft is vertical, the opposing bearing can be omitted if the bearing is adjusted clearance-free by the load in all operating states.
Axial location of the bearing rings in bearings in an adjusted or floating bearing arrangement
|
![]() |
Examples of the axial fixing of bearing rings
Axial location of bearing rings
➤ Figure to ➤ Figure show possibilities for the location of bearing rings depending on the design of the bearing arrangement and the application.
Locating/non-locating bearing arrangement
Deep groove ball bearing and cylindrical roller bearing
➤ Figure shows the bearing arrangement of the shaft in an electric motor of medium power rating.
Locating bearing A
The locating bearing A is subjected not only to radial forces but also to axial forces of alternating direction. The axial forces are not very high and do not act in a shock type manner. For location of the deep groove ball bearing, rigid shoulders, covers, snap rings or other form fit elements are therefore normally used. The adjacent parts should require little production work and mounting and dismounting should be easy to perform.
Non-locating bearing B
The non-locating bearing B must support radial forces only. The outer ring is clamped between the snap ring and cover, while the inner ring has a tight fit on the shaft.
Axial location of deep groove ball bearing and cylindrical roller bearing A = locating bearing B = non-locating bearing
|
![]() |
Locating/non-locating bearing arrangement
Tapered roller bearing pair and cylindrical roller bearing
The bearing arrangement of a pinion shaft shown in ➤ Figure is subjected to high, occasionally shock type radial and axial forces. Due to the hypoid tooth set, precise axial adjustment of the pinion against the crown gear and rigid guidance are necessary.
Locating bearing A
The locating bearing A is formed by the tapered roller bearing pair clamped from within. Since spacer rings are arranged between the inner rings, the shaft nut can be tightened to a certain torque without leading to bracing of the bearing arrangement. The axial position of the pinion relative to the crown gear is set by means of shims at the time of mounting.
Non-locating bearing B
The non-locating bearing B must support radial forces only. Due to the magnitude of the forces, both rings have tight fits. A snap ring in one annular slot of the outer ring securely prevents creep of the bearing to the left. The ribs of the bearing rings represent additional security against creep to the right. In order to prevent jamming of the bearing arrangement, the non-locating bearing must have axial clearance between the inner ring rib and the rollers.
Axial location of tapered roller bearing pair and cylindrical roller bearing A = locating bearing B = non-locating bearing
|
![]() |
Locating bearing arrangement
Cylindrical roller bearing and axial deep groove ball bearing
The locating bearing in ➤ Figure is subjected to high axial forces in both directions and the shaft must be guided axially clearance-free.
The shaft locating washer of the double direction axial deep groove ball bearing and the inner ring of the cylindrical roller bearing are axially clamped by means of an end washer. The axial deep groove ball bearing is adjusted clearance-free by means of the intermediate ring inserted with a fit.
Axial location of axial deep groove ball bearing and cylindrical roller bearing
|
![]() |
Locating bearing arrangement
Spherical roller bearing
➤ Figure shows the locating bearing for a conveyor sheave. In order that the bearing can be mounted and dismounted with ease, a withdrawal sleeve is used to locate the inner ring, which is pressed in using a hydraulic mounting method. The taper on the withdrawal sleeve is self-retaining. The end cap serves as a retainer only.
Axial location of spherical roller bearing with withdrawal sleeve
|
![]() |
Locating bearing arrangement for vertical shaft
Radial deep groove ball bearing and axial deep groove ball bearing
The vertical shaft in ➤ Figure is radially guided by a radial deep groove ball bearing and axially supported by an axial deep groove ball bearing. The snap ring functions with the disc spring to give preload and prevent lift-off when the working pressure is not directed downwards. There is some axial clearance between the disc spring when pressed flat and the snap ring. This gives easier mounting of the snap ring.
Axial location of an axial and radial deep groove ball bearing with a vertical shaft
|
![]() |
Non-locating bearing arrangement
Spherical roller bearing, location by adapter sleeve
The locating bearing in ➤ Figure must support high radial loads. When the adapter sleeve is tightened, this gives the bearing on the smooth shaft a tight fit, which prevents axial creep.
Axial location of spherical roller bearing with adapter sleeve
|
![]() |
Adjusted bearing arrangement
Tapered roller bearing pair, bearings in O arrangement, outer rings with tight fit
In wheel bearing arrangements with a rotating outer ring in accordance with ➤ Figure, not only are high radial and axial forces present but tilting moments also occur. The outer rings have a tight fit. In these sorts of hub bearing arrangements, this is important due to the circumferential load acting on the outer rings. The axial clearance of the bearing group is set by means of the fixing nut, where the loosely fitted inner ring of the outer bearing undergoes displacement.
Axial location of tapered roller bearing pair H = support spacing |
![]() |
Adjusted bearing arrangement with spring washer
Deep groove ball bearings
The example in ➤ Figure shows a bearing arrangement that is commonly used in small electric motors. The bearings are not subjected to high loads, the speed is in the moderate range. The radial load is small and only guidance forces must be supported in an axial direction.
Inner rings with tight fit, outer rings with sliding seat, bearings adjusted by means of spring preload
The inner rings of the deep groove ball bearings have a tight fit on the journal and are abutted on the shaft shoulders. The outer rings have a sliding seat. A spring washer is fitted between the outer ring of the right hand bearing and the cover collar. The bearings are axially adjusted by the tensioned springs. This achieves particularly smooth running.
Floating bearing arrangement
Spherical roller bearings
➤ Figure shows the bearing arrangement of a heavy support roller. The bearings are subjected to high radial loads. In addition, a frictional force acts axially on the outside surface of the support roller. Close axial guidance is not required and, as a result, a floating bearing arrangement can be selected. In the course of this, the lateral movement of the outer rings is restricted by the contact in the housing. Both housings are split. The axial displacement distance s can be measured with the upper section removed.
Axial location of two spherical roller bearings s = axial displacement distance
|
![]() |
Raceways with direct bearing arrangement
The raceways must be produced as a rolling bearing raceway
In rolling bearings without an inner ring, the rolling elements run directly on the shaft, while in bearings without an outer ring they run directly in the housing bore. The shaft and/or housing bore must therefore be produced as a rolling bearing raceway; steels, surface hardness and hardening depth ➤ link.
The raceways must be free of waviness and precision machined (grinding and honing); for design of raceways see product chapter.
The fits have a major influence on the bearing clearance
The shaft and housing fits have a considerable influence on the bearing and operating clearance of the rolling bearing; this must be taken into consideration in determining the tolerances.
Steels for the raceways
Through hardening steels
Through hardening steels in accordance with ISO 683-17 (e. g. 100Cr6) are suitable as materials for rolling bearing raceways in direct bearing arrangements. These can also be surface layer hardened.
Case hardening steels
Case hardening steels must conform to DIN EN ISO 683-17 (e. g. 17MnCr5, 18CrNiMo7-6) or EN 10084 (e. g. 16MnCr5).
Steels for induction surface layer hardening
For flame and induction hardening, steels to DIN EN ISO 683-17 must be used (e. g. C56E2, 43CrMo4) or DIN 17212 (e. g. Cf53).
Surface hardness and hardening depth of raceways
Nominal surface hardness: ≧ 670 HV
The hardness values apply to raceways, axial washers and shaft shoulders. Steels hardened by means of case, flame or induction hardening must have a surface hardness of 670 HV to 840 HV and an adequate hardening depth CHD or SHD.
Determining CHD and SHD
The requisite case hardening depth CHD for case hardening steels is determined in accordance with ➤ Equation, while the requisite surface hardening depth SHD for steels for induction surface layer hardening is determined in accordance with ➤ Equation.
Nominal hardening depth ≧ 0,3 mm
In accordance with DIN EN ISO 15787:2010, the hardening depth is the depth of the hardened surface zone at which there is still a hardness of 550 HV1. It is measured on the finish ground shaft and must correspond to the stated values, but must in any case be ≧ 0,3 mm.
Determining the case hardening depth
Approximation value for case hardening depth
An approximation value for determining the minimum hardness depth can be found in ➤ Equation. The reference value for the load present is the equivalent stress in accordance with the distortion energy hypothesis (DEH) as a function of the rolling element diameter Dw and the magnitude of the load.
Case hardening depth

Legend
CHD | mm |
Case hardening depth |
Dw | mm |
Rolling element diameter |
The local hardness must always be above the local requisite hardness, which can be calculated from the equivalent stress.
Case hardening depth and hardness profile HV = hardness according to Vickers z = depth under the contact surface
|
![]() |
Determining the surface hardening depth
For the calculation of the surface hardening depth SHD ➤ Equation applies.
Surface hardening depth

Legend
SHD | mm |
Surface hardening depth |
Dw | mm |
Rolling element diameter |
Rp0,2 | N/mm2 |
Yield point of base material |
Raceway hardness is less than 670 HV
If the raceway fulfils the requirements for rolling bearing materials but its hardness value is less than 670 HV (58 HRC), the load on the bearing arrangement cannot be as high as the full load carrying capacity of the bearing. In order to determine the load carrying capacity, the basic dynamic load rating C of the bearings must be multiplied by the reduction factor fH and the basic static load rating C0r by the reduction factor fH0 ➤ Figure and ➤ Figure.
Dynamic hardness factor at reduced hardness of raceways fH = dynamic hardness factor HV, HRC = surface hardness |
![]() |
Static hardness factor at reduced hardness of raceways fH0 = static hardness factor HV, HRC = surface hardness
|
![]() |